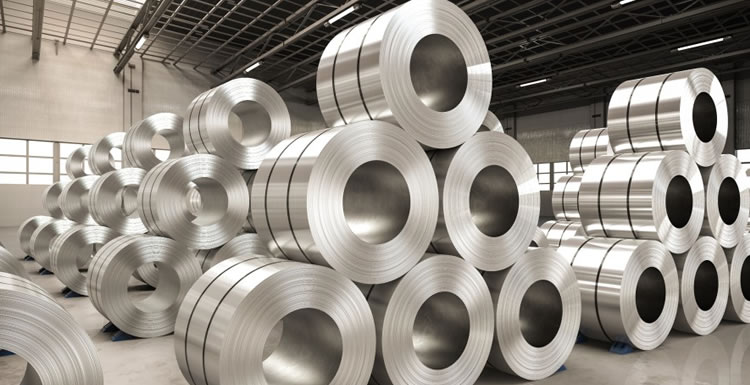
d'acier, la nécessité d'amincir la plaque d'acier. Alors que les tôles d'acier ordinaires ont généralement une épaisseur comprise entre 0,7 et 0,75 mm, les tôles super résistantes d'aujourd'hui ne mesurent que 0,65 mm ou moins, et le capot de la nouvelle opel seferli a une épaisseur de 0,6 mm.
Selon wang li, « si la gravité spécifique de l'acier n'est pas modifiée, le poids ne peut être que réduit, mais la densité peut être ajustée. Maintenant, nous avons une nouvelle idée à faire, qui consiste à ajuster la densité de l'acier. L'avantage de l'aluminium est la faible densité, la concurrence dans une certaine mesure, je peux utiliser vos avantages pour ajuster ma densité. Nous avons augmenté le module d'élasticité de l'acier. , et maintenant c'est dans le laboratoire. Un point que je veux faire est que parce que l'acier lui-même reste inchangé sur la base de l'industrie industrielle existante, il y a encore beaucoup de place pour l'innovation. De ce point de vue, l'acier a encore une certaine vitalité, ainsi que sa part de marché. Si la voiture se vend plus de 200 000 yuans, elle utilisera plus de matériaux. Si la voiture se vend 100 000 yuans, elle utilisera toujours de l'acier.
Mais le problème du coût devient également un autre matériau pour remplacer la position du corps principal de l'acier dur raison. matériaux composites légers, acier à haute résistance ou dans la position du corps principal, mais je pense que les principaux facteurs sont le coût, je crois que si le coût de la fibre de carbone, la fibre de carbone remplacera le probable, ce n'est pas impossible, la clé maintenant le coût est trop élevé, l'acier présente également à l'heure actuelle un avantage de coût très important.
En plus du coût, dans la plage de résistance pour répondre à la demande, le processus de formage bon et facile devient également la raison pour laquelle l'acier est difficile à remplacer. "Du point de vue du développement, la résistance de l'acier pour la voiture est pas très élevé. 1000 mpa suffisent. L'acier à haute résistance est maintenant principalement du carbone à renforcer, beaucoup ont fait 2200 mpa, mais au-dessus de 2200 mpa, cela produira une mutation, ou 2200-2500 mpa de carbone pour renforcer fondamentalement impossible. "Je crois que cet acier aura certainement d'autres matériaux pour remplacer le carbone, la résistance sera de plus en plus élevée, mais il n'est pas nécessairement utilisé dans la voiture, il peut être utilisé dans d'autres domaines de haute résistance.Pour les voitures, nous avons un large choix d'acier sous 1000 mpa, faible coût et très bon processus de formage, il sera donc très difficile de remplacer l'acier dans notre pays pendant un certain temps.
Et d'après les propriétés structurelles de l'acier lui-même, il a une bonne réparation. Zhu qiang a souligné que l'acier lui-même avec transition de phase présente certains avantages dans certaines applications. "Pour l'acier automobile, parce que l'acier a des transitions de phase, s'il frappe une fosse, il peut être facilement réparé, ce qui est relativement difficile pour les composites ou l'aluminium. Par exemple, un matériau composite en alliage d'aluminium, si un trou est cassé, la réparation de base est une pièce entière de remplacement, le coût est également élevé, c'est la faiblesse de l'aluminium lui-même par rapport à l'acier.
Alliage d'aluminium
période de développement rencontrée avant le loup après le tigre
Les chiffres montrent qu'il faut 725 kg d'acier et de fonte et 350 kg d'acier embouti pour fabriquer une voiture moyenne de taille moyenne. En revanche, le poids de l'aluminium dans une voiture européenne est passé de 50 kg en 1990 à 131,5 kg en 2005, le plus encore utilisé dans les composants internes du moteur et les blocs-cylindres et la montée. L'aluminium est également populaire dans les voitures car il pèse moins de la moitié du poids du fer, le matériau utilisé pour fabriquer l'acier, et a une meilleure résistance à la corrosion que l'acier.À l'heure actuelle, l'utilisation d'alliage d'aluminium pour fabriquer la carrosserie du modèle a été très répandue. Depuis sa naissance en 1994, l'audi A8 a adopté la structure de carrosserie à cadre spatial entièrement en aluminium, et le modèle S développé et fabriqué par tesla adopte également le corps tout en aluminium.Après la mise en production de la ligne de production tout en aluminium de chery jaguar land rover à changshu, dans la province du jiangsu,la première voiture domestique, le nouveau taux d'application du matériau en alliage d'aluminium jaguar XFL a atteint 75%. L'alliage d'aluminium à haute résistance nobelis RC5754 utilisé dans de nombreuses pièces de carrosserie du jaguar XFL a un rendement de 105-145 Mpa, une résistance à la traction de 220 Mpa , et une bonne performance en termes de résistance, de résistance à la corrosion, de connectivité et de taux de moulage."Maintenant, de plus en plus d'aluminium est utilisé pour les voitures, en particulier pour les pièces de châssis, en plus de la carrosserie, maintenant beaucoup de voitures continuent de marcher sur cette route. Il y a quelques problèmes avec le cadre tout en aluminium, mais ils sont en cours de résolution . "Zhang haitao, chercheur à l'université de soochow, a déclaré:" pourquoi utiliser des cadres entièrement en aluminium? Le premier coût est relativement faible, le coût d'une petite voiture peut être de quelques milliers de yuans par cadre, le plus important est la conception de la section est très complexe, et la rigidité en flexion et en torsion de l'aluminium est meilleure que l'acier.
De plus, l'aluminium a une meilleure récupération des ressources et un cycle de vie plus long que l'acier. Si l'acier est rouillé, il est très difficile à récupérer. Les alliages d'aluminium ont des avantages à long terme. Si les roues en aluminium, nous avons maintenant un consensus sur le fait que les roues en alliage d'aluminium doivent être meilleures que l'acier, car l'acier est facile à toucher la rouille, le grattage en alliage d'aluminium n'a pas d'importance, cet acier de performance n'est pas façon de comparer, les performances des composites en alliage d'aluminium à cet égard présentent un avantage unique. »En outre, le long cycle de vie est également important pour l'industrie automobile, et chaque produit doit être conçu en gardant à l'esprit le long cycle de vie. L'aluminium présente également un avantage à cet égard.
Zhu qiang a également souligné que la composition de l'alliage d'aluminium est relativement complexe, comment recycler la classification est également un problème." Par exemple, pour le cadre du moulage sous pression, les deux plaques d'alliage ne peuvent pas être utilisées ensemble, elles doivent être séparés, il faut beaucoup d'efforts pour les connecter, et il faut beaucoup d'efforts pour les séparer. D'une part, l'efficacité de récupération n'est pas élevée et, d'autre part, elle n'est pas facile à gérer. En outre, le recyclage de l'aluminium pose de nombreux problèmes, tels qu'une utilisation réduite, un bon recyclage de l'aluminium peut être utilisé. pour faire quelque chose qui n'est pas important, ce qui aurait été de bonnes choses finit par avoir une faible valeur.
En termes de propriétés de fatigue des matériaux, l'aluminium est plus risqué que l'acier, et la transformation est limitée. matériaux. La capacité d'oxydation de l'aluminium est très forte, ces défauts ont un impact relativement important sur les performances en fatigue des composants, il est très facile de se tromper. L'acier ne s'oxyde pas autant et ses défauts ont un impact relativement faible sur les performances en fatigue. dit, "seulement avec le forgeage ne peut pas être des composants complexes, le forgeage doit être traité, sinon il ne peut pas répondre aux besoins de la conception structurelle. D'une manière générale, il existe deux types de forgeage, soit en abandonnant l'optimisation structurelle, soit en refaçonnant. Cependant, une fois que la surface de l'alliage d'aluminium est endommagée, les performances de fatigue diminueront et le coût augmentera à nouveau. Ce sont les problèmes que les alliages d'aluminium doivent surmonter, et il est possible de remplacer l'acier après avoir résolu ces problèmes.
Dans le châssis automobile, l'aluminium a remplacé une partie de l'acier, mais ces dernières années, avec le développement de la technologie de l'acier, l'acier du châssis a introduit de nouvelles solutions. nous pouvons maintenant faire 780 mpa bras triangulaire en acier, il est moins de 10 pour cent plus lourd que l'aluminium, beaucoup moins cher. Il y a aussi un lien entre les deux roues qui est très lourd, et maintenant nous avons développé une nouvelle technologie qui réduit le poids de 40 pour cent et résout le problème de corrosion en utilisant des revêtements, et l'acierlui-même s'améliore. Maintenant, l'acier et l'aluminium sont en concurrence pour se promouvoir, il y a donc plus d'options pour les constructeurs automobiles, et donc le développement.
En fait, l'aluminium automobile actuel est entré dans la scène avant le loup après le tigre. Les anciens fabricants d'acier grâce à l'amélioration continue des performances, maintenant l'acier sans nickel peut atteindre la rouille, tandis que ce dernier alliage de magnésium, fibre de carbone et autres matériaux à moindre coût et des performances améliorées, ont eu un impact sur le marché de l'aluminium. dès que possible, ne sera pas facilement remplacé par plus tard, les défis et opportunités actuels de l'aluminium automobile coexistent.La structure de carrosserie hybride acier-aluminium est la tendance
À l'heure actuelle, de plus en plus d'ingénieurs de fabrication automobile accordent une plus grande attention à l'application hybride de matériaux légers. Leur recherche et développement se concentre non seulement sur le rapport spécifique de l'acier automobile et de l'aluminium, mais également sur la façon de mélanger correctement divers matériaux. innovation et mise à niveau de la technologie de la structure du corps, abandonné l'audi a toujours été fier de l'ensemble du corps en aluminium, alliage d'aluminium de pente à 58%, en plus de l'identité de, dans le matériau du corps ajouté plus de matériaux composites, le corps est près de 51 kilogrammes plus lourd que le modèle cash, par les modèles cash A8 de 236 kg « poids à contre-courant de 282 kg.
La nouvelle génération d'Audi A8 adopte l'alliage d'aluminium pour construire le cadre global de la carrosserie. Pour assurer la résistance structurelle, des pièces moulées en aluminium sont utilisées dans les joints clés et des pièces en tôle sont utilisées sur la surface de la carrosserie. Acier à haute résistance A8 uniquement dans l'application de la colonne B, le matériau en acier à haute résistance et il y a 20 ans par rapport à l'acier, la rigidité a été multipliée par 5, le poids a été réduit de 40 %. Un alliage de magnésium est ajouté à la structure de la carrosserie et de la fibre de carbone CFRP un matériau composite est utilisé à l'arrière de la voiture, ce qui réduit le poids de la carrosserie à partir de détails tels que le panneau arrière.
"A l'avenir, l'aluminium sera de plus en plus utilisé dans toute la carrosserie de la voiture, et il y aura beaucoup de carrosseries hybrides. Par exemple, la carrosserie en aluminium Audi A8 commence également à fabriquer des carrosseries hybrides, et maintenant de nombreux constructeurs automobiles nationaux emboîtent le pas. Le principal problème avec les connexions en acier et en aluminium est la résistance à la corrosion, avec collage, avec attache, sans soudure. Le haut du corps est fabriqué d'acier et le bas du corps est en aluminium.Par exemple, le cadre de la fenêtre de l'automobile de Pékin est en acier sur le dessus et en aluminium sur le fond.Ce n'est pas que l'acier soit mauvais, mais je pense qu'il est plus prometteur de mélanger l'acier avec l'aluminium. », a déclaré Zhang haitao.
À cet égard, wang li a également souligné qu'en fait, dès les années 1940, lorsqu'il y avait une concurrence entre l'acier et l'aluminium, après de nombreuses années de développement, les matériaux automobiles ont maintenant atteint un certain consensus, les bons matériaux sont-ils utilisés au bon endroit Et l'acier lui-même se développe rapidement, avec à la fois la concurrence et la coopération. Et cette concurrence est plus bénéfique pour le développement des entreprises automobiles, car l'existence d'entreprises automobiles concurrentes peut avoir plus de choix. exigences de légèreté.
La stratégie des "marques indépendantes doit être légère, un bon acier avec son potentiel n'est toujours pas petit, au moyen de marques en coentreprise avec la proportion d'acier à haute résistance et il est très facile d'atteindre 10 % de la perte de poids du corps blanc, grâce au les efforts des autres véhicules baissent de 7 % 8 % est faisable, l'identitéde la proportion de la technologie de pointe peut atteindre un corps sans changement de plus de 10%. " "Avec certaines nouvelles technologies et techniques, plus de 20 pour cent de perte de poids peuvent être atteints. Nous avons analysé de nombreux modèles de nos propres marques, et le potentiel est toujours génial. L'écart est notre motivation