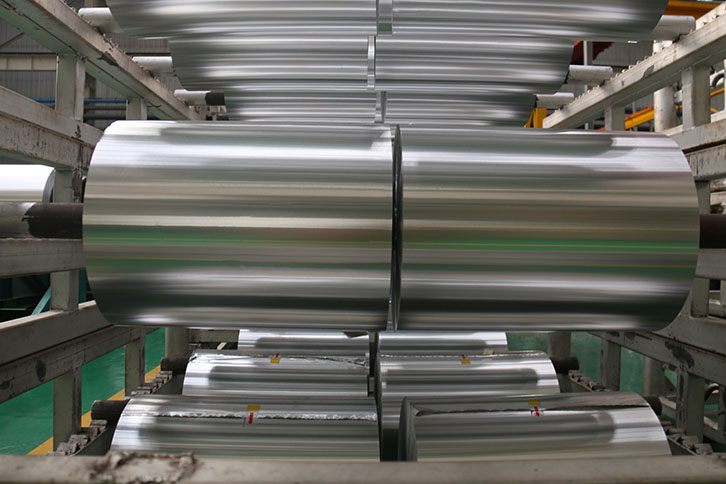
3003 aluminum coil offers superior corrosion resistance & formability for construction, packaging, and transportation. ASTM/ISO certified. Request a quote today.
READ MORE...3003 aluminum coil offers superior corrosion resistance & formability for construction, packaging, and transportation. ASTM/ISO certified. Request a quote today.
READ MORE...AOYIN METAL a high-quality aluminum plate supplier in China, has completed an export order of 44 tons of 1100 H18 aluminum plates to Vietnam and provided efficient supply chain services.
READ MORE...Discover why 20+ countries trust our 5083 H116/H321 marine aluminum plates – DNV/ABS certified, saltwater-proof, with real container shipment proof. Download free alloy guide now.
READ MORE...- Scalping: to remove surface defects such as segregation, slag inclusion, scars, and surface cracks, and improve the surface quality of the sheet. The scalping machine mills both sides and edges of the slab, with a milling speed of 0.2m/s. The maximum thickness to be milled is 6mm, and the weight of the aluminum scraps produced is 383kg per slab, with an aluminum yield of 32.8kg. - Heating: the scalped slab is then heated in a pusher-type furnace at a temperature of 350℃ to 550℃ for 5-8 hours. The furnace is equipped with 5 zones, each with a high-flow air circulation fan installed on the top. The fan operates at a speed of 10-20m/s, consuming 20m3/min of compressed air. There are also 20 natural gas burners installed on the upper part of the furnace, consuming approximately 1200Nm3/h of natural gas. - Hot Rough Rolling: the heated slab is fed into a reversible hot rolling mill, where it undergoes 5 to 13 passes to be reduced to a thickness of 20 to 160mm. - Hot Precision Rolling: the rough rolled plate is further processed in a hot precision rolling mill, with a maximum rolling speed of 480m/s. It undergoes 10 to 18 passes to produce plates or coils with a thickness of 2.5 to 16mm..
READ MORE...5052 aluminum plate for AL-Mg system alloy aluminum plate, is the most widely used kind of rustproof aluminum, high strength and corrosion resistance. Plasticity is still good in semi-cold work hardening, low plasticity in cold work hardening, can be polished. It is generally used for bodywork in tanks. General thickness ranging from 4mm-25mm, width 2000mm, length 3500-7200mm..
READ MORE...5A06 is a high magnesium alloy with good strength, good corrosion resistance and good machinability among non-heat treatable alloys. .
READ MORE...6063 aluminum alloy, with high strength and high hardness and good anodic surface oxidation treatment, is the ideal raw material for architectural and industrial aluminum profiles..
READ MORE...High Speed Rail Vehicles in Extreme Environments: Aluminum Alloy Applications and Low Temperature Performance Testing..
READ MORE...