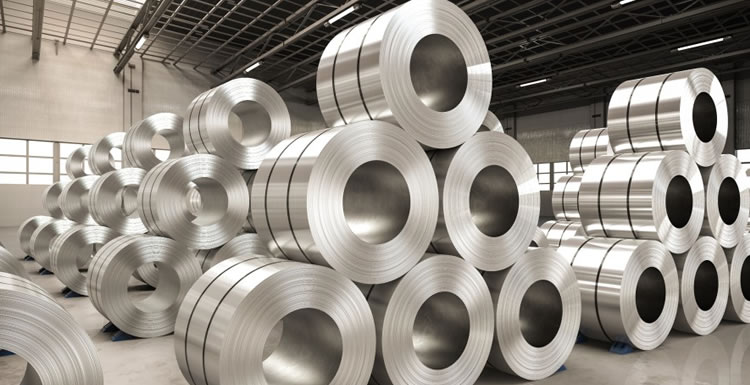
铝板卷与钢竞争
钢铁一直是汽车制造的主要材料,但随着社会对环保节能的呼声越来越高,国家油耗政策趋于收紧,消费者对汽车的安全性也提出了更高的要求,这迫使汽车制造商不得不汽车研究中心的一份报告显示,到 2020 年,高强度钢的使用量预计将达到汽车重量的近 15%。到 2040 年,这一比例将逐渐下降至近 5%,届时其他轻质材料将在汽车材料业务中占有一席之地。
铝的重量不到钢铁原材料的一半,耐腐蚀性能更好,曾经对汽车用钢构成威胁。但是,由于铝的价格相对较高,制造和维修过程困难,许多汽车制造商更愿意使用用高强度碳钢代替普通钢。于是,钢铝博弈上演。在日前举行的汽车与环保论坛上,宝钢研究院首席研究员王力、南方科技大学讲座教授朱强等业内专家,吉林大学陈树明教授、张海涛等在圆桌讨论“钢铝之争”。
钢材具有巨大的应用潜力和成本优势
随着汽车用钢的不断发展,汽车用钢已经不是几十年前很多人印象中的低碳钢了,现在汽车用钢板在减薄,但钢的强度和耐腐蚀性有了很大的提高。为了迎接新的挑战材料方面,不少钢铁生产企业积极开发轻量化高强钢,与铝合金等材料竞争节省约 5%。
高强钢在中国汽车市场的现状和应用潜力如何?王力对此进行了分析,他表示,当前汽车用钢在不断努力减轻重量,“其中使用了很多技术,其中之一贡献是高强度钢。过去20年左右,宝钢一直参与的iisa项目。如果钢厂通过开发新材料继续使用钢材,钢材的潜力有多大?经过这么多年的发展,最后给汽车厂的建议或技术,一是开发各种先进的高强度钢仍然是在路上,二是研发了很多先进的制造技术,同时引入了全生命周期的概念。比如最新开发的一款电动概念车,车身减重高达40%,它用高强度钢的强度要高一些,1000MPa以上的占40%,只有5%是软钢,这种钢通过强度潜力还是比较大的。
“从宝钢的销售数据来看,2017年中国自主品牌占高强钢消费量的41%,欧日美韩自主汽车销量超过2800万辆。宝钢提供的材料是比较高档的,我们全国平均水平会比这个水平低一点。从我们去年的数据来看,高强钢的应用率平均达到42-45%,应该是比较高的。低,国外60-70%。这个差距就是我们的潜力。”
之间的竞争铝板和钢、铝的突出优势是密度低,实现车身减重,符合比例自身也在提升。现在钢铝相互竞争,相互促进,车企有更多选择,也有发展。”
事实上,目前的汽车铝材已经进入了先狼后虎的阶段。以前的钢厂通过性能的不断提升,现在的钢不用镍就可以做到防锈,而后者的镁合金、碳纤维等材料成本更低和性能的提高,对铝市场形成了冲击。朱强指出,“铝合金要做好,只能是快速发展,因为钢做了这么多年,要替代它是困难的,铝必须工业化作为尽快,不会被以后轻易取代,当前汽车铝材的挑战与机遇并存。
钢铝混合车身结构是趋势
目前,越来越多的汽车制造工程师更加关注轻量化材料的混合应用。他们的研发重点不仅在于汽车钢铝的具体比例,还在于如何正确混合各种材料。去年在法兰克福车展上亮相的全新奥迪A8已经全部采用了奥迪的铝制空间框架型。车身结构技术创新升级,摒弃了奥迪一向引以为豪的全铝车身,铝合金的坡度达到58%,除此之外,在车身材质上加入了更多的复合材料,车身近51公斤比现款车型重,由现款A8车型的236公斤“逆势增至282公斤”。
新一代奥迪A8采用铝合金打造车身整体框架。为保证结构强度,关键接头采用铝铸件,车身表面采用钣金件。在车身的舱笼结构中,大量采用热成型超高强度合金钢,远超目前A8高强度钢只在B柱中应用,这种高强度钢材料和20年前的钢相比,刚度提高了5倍,重量减轻了40%。车身结构中加入了镁合金,以及CFRP碳纤维车尾采用复合材料,从后面板等细节减轻车身重量。
“未来,铝材在整个车身中的应用会越来越多,混合动力车身也会很多。比如奥迪A8铝制车身也开始做混合动力车身,现在国内很多车企都在效仿。钢铝连接的主要问题是耐腐蚀,有胶合,有系绳,不用焊接。钢的,下半身是铝的。比如北京汽车的窗框是上钢下铝。不是说钢不好,但我觉得钢铝混合比较有前途。 ”张海涛说。对此,王力也指出,其实早在1940年代就有钢铝竞争的时候,经过多年的发展,现在汽车材料已经达成了一些共识,就是用对了地方的合适的材料而钢铁本身也在快速发展,竞争与合作并存。而这种竞争对车企的发展更为有利,因为竞争的存在车企可以有更多的选择。展望未来,新能源汽车可能会有更高的选择轻量化的要求。
“自主品牌要轻量化,好钢潜力不小,通过合资品牌的高强钢比例很容易实现白车身减重10%,通过其他车辆的努力下降7% 8% 是可行的,认同先进技术的比例可以做到不改变10%以上。”“通过一些新技术和新技术,可以达到20%以上的减肥效果。我们分析了我们自己品牌的许多车型,潜力仍然很棒。差距是我们的动力