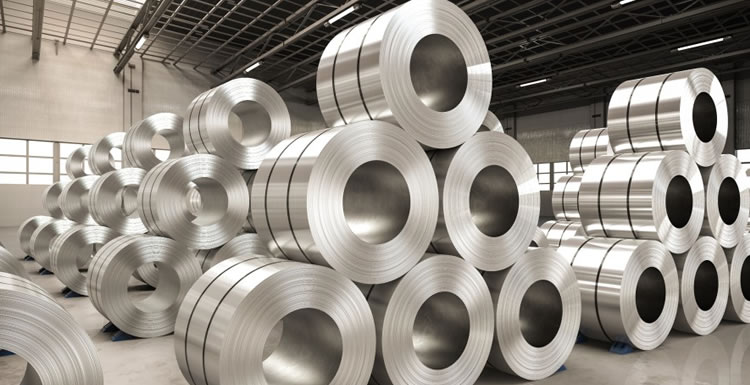
калем од алуминијумског лима се такмичи са челиком
Челик је одувек био главни материјал у производњи аутомобила. Али како је друштво за заштиту животне средине и уштеду енергије све гласније, национална политика потрошње горива тежи да се пооштрава, потрошачи такође постављају веће захтеве за безбедност возила, што је приморало произвођаче аутомобила да тражити јачи и лакши материјал за изградњу возила. Очекује се да ће употреба челика високе чврстоће достићи врхунац од скоро 15 одсто тежине возила до 2020. године, према извештају центра за аутомобилска истраживања. До 2040. тај удео ће постепено пасти на скоро 5 процената, када ће други лаки материјали имати места у послу са аутомобилским материјалима.
Са мање од половине тежине и бољом отпорношћу на корозију од сировог материјала челика, алуминијум је некада представљао претњу за аутомобилски челик. Међутим, због релативно високе цене алуминијума и потешкоћа у процесима производње и одржавања, многи произвођачи аутомобила радије замените обичан челик угљеничним челиком високе чврстоће. Стога се игра између челика и алуминијума. На недавно одржаном аутомобилском и еколошком форуму, стручњаци из индустрије као што су Ванг Ли, главни истраживач Баостеел истраживачког института, Зху Кианг, професор на катедри Јужног универзитета за науку и технологију, Цхен Схуминг, професор Јилин универзитета, зханг хаитао и тако даље, разговарали су о „такмичењу челика и алуминијума“ на округлом столу.
Челик има велики потенцијал примене и предност у трошковима
Уз континуирани развој аутомобилског челика, аутомобилски челик је пре неколико деценија био утисак многих људи о челику са ниским садржајем угљеника, сада се челична плоча за аутомобиле стањи, али је чврстоћа челика и отпорност на корозију знатно побољшана. Да би се одговорило на изазов нових материјала, многа предузећа за производњу челика активно развијају лагани челик високе чврстоће који може да се такмичи са легурама алуминијума и другим материјалима. Према подацима, само 212 евра додатних трошкова по возилу за челик високе чврстоће потребно је да би се постигло смањење тежине и горива уштеда од око 5%.
Каква је тренутна ситуација и потенцијал примене челика високе чврстоће на кинеском аутомобилском тржишту? Ванг Ли је ово анализирао, рекао је да је тренутни аутомобилски челик у сталним напорима да се смањи тежина, „који користи много технологије, један од допринос је челик високе чврстоће. У последњих 20 година постојао је ииса пројекат у коме Баостеел учествује. Ако челичане наставе да користе челик развијајући нове материјале, какав је потенцијал челика? Кроз толико година развоја, последњи савет или технологија за фабрику аутомобила је да се развије низ напредних челика високе чврстоће и даље на путу, други је да се развије много напредних производних технологија, ау исто време уведен концепт пуног животног циклуса. На пример, најновији развој електричног концепт аутомобила, смањење телесне тежине до 40%, то са високом чврстоћом челика чврстоћа је већа, више од 1000 мпа од 40%, само 5% је меки челик, челик кроз снагу овог потенцијала је још увек релативно велики.
„Према подацима о продаји баостеела, кинески брендови у сопственом власништву чинили су 41 одсто потрошње челика високе чврстоће у 2017, а продато је више од 28 милиона европских, јапанских, америчких и корејских аутомобила у сопственом власништву. Материјали које обезбеђује баостеел су релативно високог квалитета, а наш национални просек ће бити мало нижи од овог нивоа. Однос примене челика високе чврстоће достиже у просеку 42-45% према нашим подацима из прошле године, што би требало да буде релативно ниске, а 60-70% у иностранству. Овај јаз је наш потенцијал.”
Такмичење измеђуалуминијумски лими челик, изузетна предност алуминијума је ниска густина и постизање смањења телесне тежине, у складу са пропорцијомод челика, потреба за тањивањем челичне плоче. Док су обични челични лимови обично дебљине између 0,7 и 0,75 мм, данашњи лимови супер чврстоће су само 0,65 мм или тањи, а хауба новог Опел сеферлија је дебљине 0,6 мм.
Према Ванг Лију, „ако се специфична тежина челика не промени, тежина се може смањити само на тање, али се густина може подесити. Сада имамо нову идеју да урадимо, а то је да прилагодимо густину челика. Предност алуминијума је ниска густина, конкуренција у одређеној мери могу да искористим ваше предности да прилагодим своју густину. Повећали смо модул еластичности челика , а сада је у лабораторији. Једна ствар коју желим да нагласим је да због тога што сам челик остаје непромењен на основу постојеће индустријске индустрије, још увек има много простора за иновације. Из ове перспективе, челик још увек има одређену виталност, као и свој удео на тржишту. Ако се аутомобил прода за више од 200.000 јуана, користиће више материјала. Ако се аутомобил прода за 100.000 јуана, и даље ће користити челик.
Али проблем трошкова такође постаје други материјал који ће заменити главни положај тела челичним чврстим разлогом. Шу-минг Чен је рекао, „под трендом смањења тежине аутомобила, иако сада сви раде лаке материјале, као што су легура алуминијума, легуре магнезијума и други лаки композитни материјали, челик високе чврстоће или у главном положају тела, али мислим да је главни фактор цена, верујем да ако ће цена угљеничних влакана, угљенична влакна заменити вероватно, није немогуће, кључна цена је сада превисоко, челик тренутно такође има веома велику предност у трошковима."
Поред цене, у опсегу чврстоће да се задовољи потражња, добар и лак процес формирања такође постаје разлог зашто је челик тешко заменити.” Са развојне тачке гледишта, снага челика за аутомобил је не много висока. 1000 мпа је довољно. Челик високе чврстоће је сада углавном угљеник за јачање, многи су радили 2200 мпа, али изнад 2200 мпа, произвешће мутацију, или 2200-2500 мпа угљеник за ојачање у основи немогуће.” Верујем да ће овај челик дефинитивно имати други материјали који замењују угљеник, снага ће бити све већа и већа, али не мора се користити у аутомобилу, може се користити у другим областима високе чврстоће. За аутомобиле имамо широк избор челика испод 1000 мпа, ниске цена и веома добар процес формирања, тако да ће неко време бити веома тешко заменити челик у нашој земљи.
А што се тиче структурних својстава самог челика, он има добру поправку. Зху кианг је истакао да сам челик са фазним прелазом има неке предности у неким применама.” За аутомобилски челик, пошто челик има фазне прелазе, ако удари у јаму, може се лако поправити, што је релативно тешко за композите или алуминијум. На пример, композитни материјал од легуре алуминијума, ако је рупа сломљена, основна поправка је цео комад замене, цена је такође висока, ово је слабост сам алуминијум у поређењу са челиком.
Легура алуминијумаразвојни период настао пре Вука после тигра
Бројке показују да је за израду просечног аутомобила средње величине потребно 725 килограма челика и ливеног гвожђа и 350 килограма штанцаног челика. Насупрот томе, тежина алуминијума у европском аутомобилу порасла је са 50 кг 1990. на 131,5 кг 2005. већина се још увек користи у унутрашњости мотора и блоковима цилиндара и расте. Алуминијум је такође популаран у аутомобилима јер је мањи од половине тежине гвожђа, материјала који се користи за прављење челика, и има бољу отпорност на корозију од челика.
Тренутно се користи алуминијумска легура за израду каросерије модела. Од свог рођења 1994. године, ауди А8 је усвојио структуру каросерије од потпуно алуминијумског свемирског оквира, а Модел С је развила и произвела Тесла такође усваја потпуно алуминијумско тело. Након потпуно алуминијумске производне линије Цхери Јагуар Ланд Ровер у Чангшуу, провинција Ђангсу је пуштена у производњу,први домаћи аутомобил, нови јагуар КСФЛ материјал од легуре алуминијума, стопа примене материјала достигла је 75%. Нобелис РЦ5754 алуминијумска легура високе чврстоће која се користи у многим деловима каросерије јагуара КСФЛ има принос од 105-145 Мпа, затезну чврстоћу од 220 Мпа , и добре перформансе у снази, отпорности на корозију, повезаности и брзини обликовања.
„Сада се све више алуминијума користи за аутомобиле, посебно за делове шасије, поред каросерије, сада доста аутомобила наставља да хода овим путем. Постоје неки проблеми са потпуно алуминијумским рамом, али они се решавају .”Зханг хаитао, истраживач на универзитету Сооцхов, рекао је, „зашто користити потпуно алуминијумске оквире? Први трошак је релативно низак, цена малог аутомобила може бити неколико хиљада јуана по оквиру, најважнији је дизајн секције је веома сложен, а алуминијумска крутост на савијање и торзиона је боља од челика.
Поред тога, алуминијум има бољи опоравак ресурса и дужи животни циклус од челика. Зху Кианг је рекао: „Стопа губитка алуминијума при рециклирању је само 5 до 10 процената. Ако је челик зарђао, веома га је тешко опоравити. Алуминијумске легуре имају предности на дуге стазе. Ако су точкови са алуминијумом, сада имамо консензус да алуминијумски точкови морају бити бољи од челика, јер челик лако додирује рђу, стругање од легуре алуминијума није битно, овај челик за перформансе није на начин да се упореди, перформансе композита алуминијумске легуре у овом погледу имају јединствену предност.” Поред тога, дуг животни циклус је такође важан за аутомобилску индустрију, а сваки производ мора бити дизајниран имајући на уму дуг животни циклус. Алуминијум такође има предност у овом погледу.”
Зху кианг је такође истакао да је састав легуре алуминијума релативно сложен, а како рециклирати класификацију је такође проблем.” На пример, за оквир ливења под притиском, две плоче од легуре се не могу користити заједно, оне морају бити раздвојени, потребно је много труда да се споје, а потребно је много труда да се раздвоје. С једне стране, ефикасност опоравка није висока, ас друге стране, није лако управљати њоме. Поред тога, постоји много проблема везаних за рециклажу алуминијума, као што је смањена употреба, може се користити добра рециклажа алуминијума да нешто што није важно, оно што би било добро заврши са малом вредношћу.”
Што се тиче особина материјала на замор, алуминијум је ризичнији од челика, а обрада је ограничена.“ Перформансе замора кључних компоненти возила контролишу се не само особинама самих материјала, већ и дефектима материјала. материјали. Капацитет оксидације алуминијума је веома јак, ови дефекти имају релативно велики утицај на перформансе замора компоненти, врло је лако погрешити. Челик не оксидира толико и његови дефекти имају релативно мали утицај на перформансе замора.” Зху кианг рекао је, „само код ковања не могу бити сложене компоненте, ковање мора бити обрађено, иначе не може задовољити потребе конструкцијског дизајна. Уопштено говорећи, постоје две врсте ковања, или одустајање од оптимизације структуре или поновна обрада. Међутим, када је површина легуре алуминијума оштећена, перформансе замора ће опасти, а цена ће поново порасти. Ово су проблеми које легуре алуминијума треба да превазиђу, а могуће је заменити челик након решавања ових проблема.”
У аутомобилској шасији, алуминијум је заменио нешто челика, али последњих година са развојем технологије челика, челик за шасије је увео нова решења. Зху кианг је рекао: „Сада шасија са челиком, развили смо неколико технологија, једна је рука, ми сада до 780 мпа сада можемо да радимо челичну троугласту руку, мање је од 10 процената тежа од алуминијума, много нижа цена. Постоји и веза између два точка која је веома тешка, а сада смо развили нову технологију која смањује тежине за 40 одсто и решава проблем корозије коришћењем премаза и челикасама се побољшава. Сада се челик и алуминијум такмиче да промовишу једни друге, тако да постоји више опција за аутомобилске компаније, а самим тим и развој.”
У ствари, садашњи аутомобилски алуминијум је ушао у фазу пре Вука после тигра. Бивши произвођачи челика кроз континуирано побољшање перформанси, сада челик без никла може да постигне рђу, док други од легуре магнезијума, угљеничних влакана и других материјала са нижим трошковима и побољшане перформансе, утицали су на тржиште алуминијума. Зху кианг је истакао, „да би легура алуминијума радила добро, може се само брзо развијати, јер челик ради толико година да га замени је тешко, алуминијум мора бити индустријализација као што је пре могуће, неће бити лако замењени касније, тренутни аутомобилски алуминијумски изазови и могућности коегзистирају.
Челик-алуминијум хибридна структура каросерије је тренд
Тренутно, све више инжењера у производњи аутомобила посвећује више пажње хибридној примени лаких материјала. Њихов фокус истраживања и развоја није само на специфичном односу аутомобилског челика и алуминијума, већ и на томе како правилно мешати различите материјале. Прошле године на сајму аутомобила у Франкфурту деби на новом аудију А8 је био аудијев алуминијумски просторни оквир. структура каросерије технологија иновација и надоградња, напуштен ауди је увек био поносан на целу алуминијумску каросерију, алуминијумску легуру нагиба до 58%, поред идентитета, у материјал каросерије додато више композитних материјала, каросерија је скоро 51 килограм тежи од готовинског модела, код кеш модела А8 од 236 кг „супротне тежине до 282 кг.
Нова генерација Аудија А8 користи легуру алуминијума за изградњу целокупног оквира каросерије. Да би се обезбедила чврстоћа конструкције, алуминијумски одливци се користе у кључним спојевима, а делови од лима се користе на површини каросерије. У кавезној структури каросерије налази се велики број легираних челика супер високе чврстоће, који се формирају вруће, далеко више од тренутног А8 челик високе чврстоће само у примени Б стуба, челичног материјала високе чврстоће и пре 20 година у поређењу са челиком, крутост је повећана 5 пута, тежина смањена за 40%. Легуре магнезијума додају се структури каросерије, а ЦФРП карбонска влакна Композитни материјал се користи у задњем делу аутомобила, што смањује тежину каросерије од таквих детаља као што је задњи панел.
„У будућности ће се алуминијум све више користити у целој каросерији аутомобила, а биће и много хибридних каросерија. На пример, ауди А8 алуминијумска каросерија почиње да прави и хибридне каросерије, а сада то следе многе домаће аутомобилске компаније. Главни проблем челичних и алуминијумских спојева је отпорност на корозију, са лепљењем, са везом, без заваривања. од челика, а доњи део тела је направљен од алуминијума. На пример, оквир прозора аутомобила у Пекингу је направљен од челика на врху и алуминијума на дну. Није да је челик лош, али мислим да је више обећавајуће мешати челик са алуминијумом. “, рекао је Зханг Хаитао.
С тим у вези, Ванг Ли је такође истакао да је у ствари, још 1940-их година када је постојала конкуренција челика и алуминијума, након много година развоја, сада су аутомобилски материјали постигли одређени консензус, прави материјали који се користе на правом месту. .И сам челик се брзо развија, и конкуренцијом и сарадњом. И ова конкуренција је кориснија за развој аутомобилских предузећа, јер постојање конкуренције аутомобилска предузећа могу имати више избора. Гледајући у будућност, нова енергетска возила могу имати више захтеви за лаку тежину.
Стратегија „независних брендова мора бити лагана, добар челик са својим потенцијалом још увек није мали, уз помоћ заједничких предузећа брендова са уделом челика високе чврстоће и врло је лако постићи 10% губитка телесне тежине белог, кроз напори других возила пад 7% 8% је изводљиво, идентитет