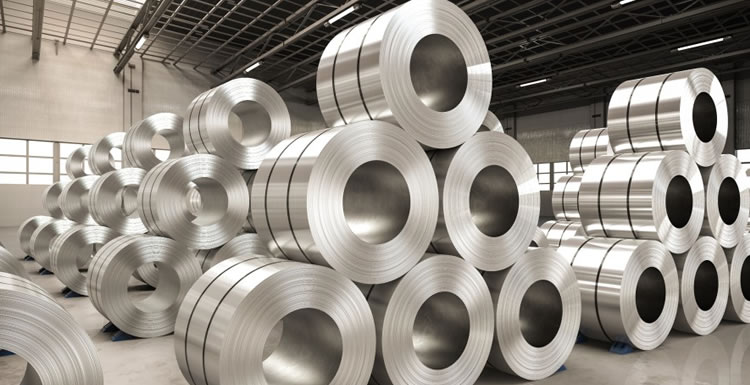
zvitok hliníkového plechu konkuruje oceli
Oceľ bola vždy hlavným materiálom vo výrobe automobilov. Ale so stále silnejším hlasom spoločnosti v oblasti ochrany životného prostredia a úspor energie, národná politika spotreby paliva má tendenciu sprísňovať sa, spotrebitelia tiež kladú vyššie požiadavky na bezpečnosť vozidiel, čo prinútilo výrobcov automobilov hľadať pevnejšie a ľahšie stavebné materiály pre vozidlá. Podľa správy Centra pre automobilový výskum sa očakáva, že používanie ocele s vysokou pevnosťou dosiahne do roku 2020 vrchol takmer 15 percent hmotnosti vozidla. Do roku 2040 tento podiel postupne klesne na takmer 5 percent, keď ostatné ľahké materiály budú mať miesto v biznise s automobilovými materiálmi.
S menej ako polovičnou hmotnosťou a lepšou odolnosťou proti korózii ako surovina ocele, hliník kedysi predstavoval hrozbu pre automobilovú oceľ. Avšak kvôli relatívne vysokej cene hliníka a ťažkostiam pri výrobe a údržbe mnohí výrobcovia automobilov uprednostňujú nahradiť obyčajnú oceľ vysokopevnostnou uhlíkovou oceľou. Preto sa hrá hra medzi oceľou a hliníkom. Na automobilovom a environmentálnom fóre, ktoré sa nedávno konalo, odborníci v tomto odvetví, ako napríklad wang li, hlavný výskumník výskumného inštitútu baosteel, zhu qiang, profesor južnej univerzity vedy a techniky, Chen shuming, profesor univerzity v Jilin, zhang haitao a tak ďalej diskutovali o „súťaži ocele a hliníka“ na okrúhlom stole.
Oceľ má veľký aplikačný potenciál a nákladovú výhodu
S neustálym vývojom automobilovej ocele nie je automobilová oceľ pred niekoľkými desaťročiami vnímaná mnohými ľuďmi ako nízkouhlíková oceľ, teraz sa automobilový oceľový plech stenčuje, ale pevnosť ocele a odolnosť proti korózii sa výrazne zlepšila. S cieľom splniť výzvu nových materiály, mnohé podniky vyrábajúce oceľ aktívne vyvíjajú ľahkú a vysokopevnostnú oceľ, ktorá môže konkurovať hliníkovej zliatine a iným materiálom. Podľa údajov je na dosiahnutie úbytku hmotnosti a paliva potrebných len 212 eur dodatočných nákladov na vozidlo na vysokopevnostnú oceľ úspora asi 5 %.
Aká je súčasná situácia a potenciál použitia vysokopevnostnej ocele na čínskom automobilovom trhu? Wang li to analyzoval a povedal, že súčasná automobilová oceľ v neustálom úsilí o zníženie hmotnosti, „ktorá využíva množstvo technológií, jednu z Príspevok je vysokopevná oceľ. Za posledných približne 20 rokov existuje projekt iisa, na ktorom sa zúčastňuje baosteel. Ak budú oceliarne aj naďalej používať oceľ vývojom nových materiálov, aký je potenciál ocele? Počas toľkých rokov vývoja, poslednej rady alebo technológie pre automobilový závod, je stále potrebné vyvíjať rôzne pokročilé vysokopevnostné ocele Druhým je vývoj mnohých pokrokových výrobných technológií a zároveň predstavenie konceptu plného životného cyklu. Napríklad najnovší vývoj elektromobilu, zníženie hmotnosti karosérie až o 40 %, s vysokou pevnosťou ocele pevnosť je vyššia, viac ako 1000 mpa o 40%, len 5% je mäkká oceľ, oceľ cez pevnosť tohto potenciálu je stále relatívne veľký.
„Z údajov o predaji baosteelu, čínske vlastné značky predstavovali 41 % spotreby vysokopevnostnej ocele v roku 2017 a predalo sa viac ako 28 miliónov európskych, japonských, amerických a kórejských vlastných áut. Materiály, ktoré poskytuje baosteel, sú relatívne vysokej kvality a náš národný priemer bude o niečo nižší ako táto úroveň. Aplikačný pomer ocele s vysokou pevnosťou dosahuje v priemere 42 – 45 % z našich údajov za minulý rok, čo by malo byť relatívne nízka a 60 – 70 % v zahraničí. Táto medzera je náš potenciál."
Súťaž medzihliníkový plecha ocele, vynikajúcou výhodou hliníka je nízka hustota a dosiahnutie zníženia telesnej hmotnosti v súlade s pomeromocele, potreba stenčiť oceľový plech. Zatiaľ čo obyčajné oceľové plechy majú zvyčajne hrúbku medzi 0,7 a 0,75 mm, dnešné super pevné plechy majú hrúbku iba 0,65 mm alebo tenšie a kapota nového Opel seferli má hrúbku 0,6 mm.
Podľa wang li „ak sa špecifická hmotnosť ocele nezmení, hmotnosť sa môže iba znížiť na tenšie, ale hustota sa dá upraviť. Teraz máme nový nápad, ktorým je úprava hustoty ocele. Výhodou hliníka je nízka hustota, konkurencia do určitej miery môžem využiť vaše výhody na úpravu mojej hustoty. Zvýšili sme modul pružnosti ocele , a teraz je to v laboratóriu. Chcem upozorniť na to, že keďže samotná oceľ zostáva nezmenená na základe existujúceho priemyselného odvetvia, stále je tu veľký priestor pre inovácie. Z tohto pohľadu má oceľ stále určitú životaschopnosť, rovnako ako jej podiel na trhu. Ak sa auto predáva za viac ako 200 000 juanov, spotrebuje viac materiálov. Ak sa auto predá za 100 000 juanov, stále bude používať oceľ.“
Problémom s nákladmi sa však stáva aj iný materiál, ktorý nahrádza hlavnú časť tela oceľovým tvrdým dôvodom. Shu-ming Chen povedal: „Podľa trendu odľahčovania automobilov, aj keď teraz každý robí ľahké materiály, ako je hliníková zliatina, horčíková zliatina a iné. ľahké kompozitné materiály, vysokopevnostná oceľ alebo v hlavnej polohe tela, ale myslím si, že hlavnými faktormi sú náklady, verím, že ak náklady na uhlíkové vlákna, uhlíkové vlákna nahradia pravdepodobné, nie je to nemožné, kľúčom sú teraz náklady príliš vysoká oceľ má v súčasnosti tiež veľmi veľkú nákladovú výhodu.“
Okrem nákladov, v rámci rozsahu pevnosti na uspokojenie dopytu, sa dobrý a jednoduchý proces tvarovania stáva tiež dôvodom, prečo je ťažké nahradiť oceľ.“ Z vývojového hľadiska je pevnosť ocele pre automobil nie veľmi vysoká. 1000 mpa je dosť.Vysokopevná oceľ je teraz hlavne uhlíková na spevnenie, mnohí urobili 2200 mpa, ale nad 2200 mpa, vytvoria mutáciu, alebo 2200-2500 mpa uhlík na spevnenie je v podstate nemožné.“ Verím, že táto oceľ určite bude mať iné materiály na nahradenie uhlíka, pevnosť bude vyššia a vyššia, ale nemusí sa nevyhnutne použiť v aute, môže sa použiť v iných oblastiach s vysokou pevnosťou. Pre autá máme široký výber ocele pod 1000 mpa, nízka náklady a veľmi dobrý proces tvárnenia, takže nahradiť oceľ v našej krajine bude chvíľu veľmi ťažké.“
A čo sa týka štrukturálnych vlastností samotnej ocele, má dobrú opravu. Zhu qiang poukázal na to, že samotná oceľ s fázovým prechodom má v niektorých aplikáciách určité výhody.“ Pre automobilovú oceľ, pretože oceľ má fázové prechody, ak narazí na jamu, dá sa ľahko opraviť, čo je pri kompozitoch alebo hliníku pomerne náročné. Napríklad kompozitný materiál z hliníkovej zliatiny, ak sa zlomí diera, základná oprava je celý kus náhrady, cena je tiež vysoká, to je slabina samotný hliník v porovnaní s oceľou.
Hliníková zliatinavývojové obdobie pred vlkom po tigrovi
Čísla ukazujú, že na výrobu priemerného auta strednej veľkosti je potrebných 725 kilogramov ocele a liatiny a 350 kilogramov lisovanej ocele. Naproti tomu hmotnosť hliníka v európskom aute vzrástla z 50 kg v roku 1990 na 131,5 kg v roku 2005. najviac sa stále používa vo vnútorných častiach motorov a blokoch valcov a stúpaní. Hliník je obľúbený aj v automobiloch, pretože má menej ako polovicu hmotnosti železa, materiálu používaného na výrobu ocele, a má lepšiu odolnosť proti korózii ako oceľ.
V súčasnosti sa na výrobu karosérie tohto modelu často používa hliníková zliatina. Od svojho zrodu v roku 1994 si Audi A8 osvojilo celohliníkovú konštrukciu karosérie s priestorovým rámom a Model S vyvinula a vyrobila spoločnosť Tesla. prijíma aj celohliníkové telo. Po celohliníkovej výrobnej linke chery jaguar land rover v meste Changshu bola uvedená do výroby provincia Jiangsu,prvý domáci automobil, nový jaguar XFL z hliníkovej zliatiny, miera aplikácie materiálu dosiahla 75 %. Nobelis RC5754 vysokopevná hliníková zliatina používaná v mnohých častiach karosérie Jaguaru XFL má výťažnosť 105-145 Mpa, pevnosť v ťahu 220 Mpa a dobrý výkon z hľadiska pevnosti, odolnosti proti korózii, konektivity a rýchlosti tvarovania.
„Teraz sa čoraz viac hliníka používa na autá, najmä na časti podvozku, okrem karosérie teraz veľa áut naďalej chodí po tejto ceste. S celohliníkovým rámom sú nejaké problémy, ale pracuje sa na nich .“ Zhang haitao, výskumník na univerzite v Soochow, povedal: „Prečo používať celohliníkové rámy? Prvé náklady sú relatívne nízke, náklady na malé auto môžu byť niekoľko tisíc juanov za rám, najdôležitejší je dizajn sekcie je veľmi zložitý a ohyb hliníka a torzná tuhosť sú lepšie ako oceľ.
Okrem toho má hliník lepšiu obnovu zdrojov a dlhší životný cyklus ako oceľ. Zhu Qiang povedal: „Miera strát pri recyklácii hliníka je len 5 až 10 percent. Ak je oceľ zhrdzavená, je veľmi ťažké ju obnoviť. Hliníkové zliatiny majú výhody z dlhodobého hľadiska. Ak sú kolesá s hliníkom, teraz máme konsenzus, že kolesá z hliníkovej zliatiny musia byť lepšie ako oceľové, pretože oceľ je ľahko na dotyk hrdzavá, škrabanie hliníkovej zliatiny nevadí, táto výkonná oceľ nie je na porovnanie, výkon kompozitu z hliníkovej zliatiny má v tomto smere jedinečnú výhodu.“ Okrem toho je pre automobilový priemysel dôležitý aj dlhý životný cyklus a každý výrobok musí byť navrhnutý s ohľadom na dlhý životný cyklus. Hliník má v tomto smere tiež výhodu.“
Zhu qiang tiež poukázal na to, že zloženie hliníkovej zliatiny je pomerne zložité, problémom je aj to, ako klasifikáciu recyklovať.“ Napríklad v rámci tlakového liatia nie je možné použiť dve zliatinové platne spolu, musia byť oddelené, ich spojenie si vyžaduje veľa úsilia a ich oddelenie si vyžaduje veľa úsilia. Na jednej strane účinnosť zhodnocovania nie je vysoká a na druhej strane nie je ľahké ju riadiť. Okrem toho existuje veľa problémov spojených s recykláciou hliníka, ako napríklad znížená spotreba, dobrá recyklácia hliníka vytvoriť niečo, čo nie je dôležité, to, čo by bolo dobré, skončí s nízkou hodnotou.“
Z hľadiska únavových vlastností materiálov je hliník rizikovejší ako oceľ a spracovanie je obmedzené.“ Únavový výkon kľúčových komponentov vozidiel je riadený nielen vlastnosťami samotných materiálov, ale aj chybami materiály.Oxidačná kapacita hliníka je veľmi silná, tieto defekty majú relatívne veľký vplyv na únavové vlastnosti komponentov, veľmi ľahko sa pokazia.Oceľ toľko neoxiduje a jej defekty majú relatívne nízky vplyv na únavové vlastnosti.“ Zhu qiang povedal: „iba s kovaním nemôžu byť zložité komponenty, kovanie musí byť spracované, inak nemôže spĺňať potreby konštrukčného návrhu. Vo všeobecnosti existujú dva druhy kovania, a to buď vzdanie sa konštrukčnej optimalizácie alebo prepracovania. Akonáhle sa však povrch hliníkovej zliatiny poškodí, únavový výkon sa zníži a náklady sa opäť zvýšia. Toto sú problémy, ktoré musia hliníkové zliatiny prekonať a po vyriešení týchto problémov je možné nahradiť oceľ.“
V automobilovom podvozku hliník nahradil časť ocele, ale v posledných rokoch s rozvojom technológie ocele zaviedla oceľ podvozku nové riešenia. Zhu qiang povedal: „Teraz podvozok s oceľou sme vyvinuli niekoľko technológií, jednou je rameno, teraz do 780 mpa teraz dokážeme vyrobiť oceľové trojuholníkové rameno, je o menej ako 10 percent ťažšie ako hliník, oveľa nižšie náklady. Existuje tiež spojenie medzi dvoma kolesami, ktoré je veľmi ťažké, a teraz sme vyvinuli novú technológiu, ktorá znižuje hmotnosť o 40 percent a problém korózie rieši použitím povlakov a oceleOceľ a hliník sa teraz navzájom presadzujú, takže automobilové spoločnosti a tým aj vývoj majú viac možností.“
V skutočnosti súčasný automobilový hliník vstúpil do štádia pred vlkom po tigrovi. Bývalí výrobcovia ocele prostredníctvom neustáleho zlepšovania výkonu môžu teraz oceľ bez niklu dosiahnuť hrdzu, zatiaľ čo tí druhí zliatiny horčíka, uhlíkových vlákien a iných materiálov s nižšími nákladmi a zlepšený výkon mali vplyv na trh s hliníkom. Zhu qiang poukázal na to, že „zliatina hliníka, aby sa dobre darilo, môže byť len rýchlym vývojom, pretože oceľ sa už mnoho rokov snaží nahradiť ju ťažko, hliník musí byť industrializovaný ako čo najskôr, nebudú ľahko nahraditeľné neskôr, súčasné výzvy a príležitosti automobilového hliníka sú koexistujúce.
Trendom je hybridná konštrukcia karosérie oceľ – hliník
V súčasnosti stále viac a viac inžinierov v oblasti výroby automobilov venuje väčšiu pozornosť hybridnej aplikácii ľahkých materiálov. Ich výskum a vývoj sa zameriavajú nielen na špecifický pomer automobilovej ocele a hliníka, ale aj na to, ako správne miešať rôzne materiály. Minulý rok na autosalóne vo Frankfurte debutoval nový audi A8 s hliníkovým priestorovým rámom audi. Inovácia technológie konštrukcie karosérie a modernizácia, opustilo audi sa vždy pýšilo celou hliníkovou karosériou, hliníkovou zliatinou sklonu až 58%, okrem identity, v materiáli karosérie pribudli ďalšie kompozitné materiály, karoséria má takmer 51 kilogramov ťažší ako hotovostný model, pri hotovostných modeloch A8 s hmotnosťou 236 kg „oproti hmotnosti 282 kg.
Nová generácia audi A8 využíva hliníkovú zliatinu na vytvorenie celkového rámu karosérie. Na zabezpečenie konštrukčnej pevnosti sú v kľúčových spojoch použité hliníkové odliatky a na povrchu karosérie sú použité plechové diely. V klietkovej konštrukcii karosérie je veľké množstvo za tepla tvárnenej super vysokopevnostnej legovanej ocele, oveľa viac ako v súčasnosti Vysokopevnostná oceľ A8 len pri použití stĺpika B, materiál ocele s vysokou pevnosťou a pred 20 rokmi v porovnaní s oceľou 5-násobne zvýšená tuhosť, znížená hmotnosť o 40 %. Do konštrukcie karosérie sa pridáva horčíková zliatina a uhlíkové vlákno CFRP v zadnej časti auta je použitý kompozitný materiál, ktorý znižuje hmotnosť karosérie od takých detailov, ako je zadný panel.
„V budúcnosti sa bude hliník čoraz viac používať v celej karosérii auta a bude veľa hybridných karosérií. Napríklad hliníková karoséria audi A8 začína vyrábať aj hybridné karosérie a teraz ich nasleduje mnoho domácich automobiliek. Hlavným problémom oceľových a hliníkových spojov je odolnosť proti korózii, s lepením, s popruhom, bez zvárania. Vrchná časť karosérie je vyrobená z ocele a spodná časť karosérie je vyrobená z hliníka. Napríklad rám okna automobilu v Pekingu je zvrchu vyrobený z ocele a zospodu z hliníka. Oceľ nie je zlá, ale myslím si, že je sľubnejšie miešať oceľ s hliníkom. “povedal Zhang haitao.
V tejto súvislosti wang li tiež poukázal na to, že už v 40-tych rokoch minulého storočia, keď existovala konkurencia ocele a hliníka, po mnohých rokoch vývoja, teraz automobilové materiály dosiahli určitý konsenzus, sú tie správne materiály používané na správnom mieste. .A samotná oceľ sa rýchlo rozvíja, s konkurenciou aj spoluprácou. A táto konkurencia je prospešnejšia pre rozvoj automobilových podnikov, pretože existencia konkurenčných automobilových podnikov môže mať viac možností. Pri pohľade do budúcnosti môžu mať nové energetické vozidlá vyššiu požiadavky na ľahkú hmotnosť.
Stratégia „nezávislých značiek musí byť ľahká, dobrá oceľ s jej potenciálom stále nie je malý, prostredníctvom joint venture značiek s podielom vysokopevnostnej ocele a je veľmi jednoduché dosiahnuť 10% úbytok hmotnosti bielej karosérie, prostredníctvom tzv. úsilie iných vozidiel pokles 7% 8% je realizovateľný, identitapodiel pokročilých technológií dokáže dosiahnuť telo bez zmeny viac ako 10 %.“ „S niektorými novými technológiami a technikami je možné dosiahnuť viac ako 20-percentný úbytok hmotnosti. Analyzovali sme mnoho modelov našich vlastných značiek a potenciál je stále skvelý. Medzera je našou motiváciou