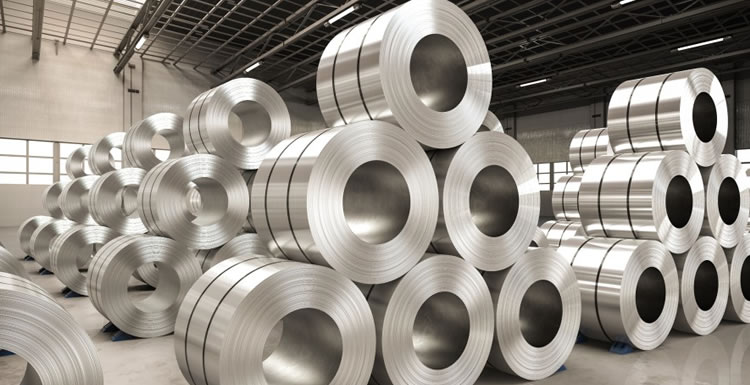
рулон алюминиевого листа конкурирует со сталью
Сталь всегда была основным материалом в автомобилестроении. Но по мере того, как общество все больше высказывалось за защиту окружающей среды и энергосбережение, национальная политика в отношении расхода топлива имеет тенденцию к ужесточению, потребители также выдвигают более высокие требования к безопасности транспортных средств, что вынуждает автопроизводителей искать более прочные и легкие материалы для изготовления транспортных средств. Согласно отчету Центра автомобильных исследований, к 2020 году ожидается, что использование высокопрочной стали достигнет почти 15% веса автомобиля. К 2040 году эта доля постепенно упадет до почти 5 процентов, когда другие легкие материалы будут использоваться в производстве автомобильных материалов.
Обладая менее чем вдвое меньшим весом и лучшей коррозионной стойкостью, чем исходный материал из стали, алюминий когда-то представлял угрозу для автомобильной стали. Однако из-за относительно высокой цены на алюминий и сложности процессов производства и обслуживания многие производители автомобилей предпочитают заменить обычную сталь высокопрочной углеродистой сталью. Таким образом, игра между сталью и алюминием разыграна. На недавно состоявшемся автомобильном и экологическом форуме эксперты отрасли, такие как Ван Ли, главный научный сотрудник научно-исследовательского института Baosteel, Чжу Цян, заведующий кафедрой, профессор Южного университета науки и технологий, Чэнь Шумин, профессор Цзилиньского университета, Чжан Хайтао и другие обсудили «конкуренцию стали и алюминия» за круглым столом.
Сталь имеет большой потенциал применения и преимущество в цене
С непрерывным развитием автомобильной стали, автомобильная сталь не несколько десятилетий назад произвела впечатление многих людей на низкоуглеродистую сталь, теперь листовая автомобильная сталь истончается, но прочность стали и коррозионная стойкость значительно улучшены. материалы, многие предприятия по производству стали активно разрабатывают легкую и высокопрочную сталь, которая может составить конкуренцию алюминиевому сплаву и другим материалам. Согласно цифрам, для достижения снижения веса и расхода топлива требуется всего 212 евро дополнительных затрат на одно транспортное средство для высокопрочной стали. экономия около 5%.
Какова текущая ситуация и потенциал применения высокопрочной стали на автомобильном рынке Китая? Ван Ли проанализировал это, он сказал, что нынешняя автомобильная сталь в непрерывных усилиях по снижению веса, «в которых используется множество технологий, одна из вкладом является высокопрочная сталь. В течение последних 20 лет или около того существовал проект iisa, в котором участвовала компания baosteel. Если сталелитейные заводы продолжают использовать сталь, разрабатывая новые материалы, каков потенциал стали? После стольких лет развития последний совет или технология для автозавода — разработать различные передовые высокопрочные стали. на пути, во-вторых, разработать множество передовых технологий производства, и в то же время внедрить концепцию полного жизненного цикла. Например, последняя разработка электрического концепт-кара, снижение массы тела до 40%, это с высокопрочной сталью прочность выше, более 1000 МПа на 40%, только 5% составляет мягкая сталь, сталь благодаря прочности этого потенциала по-прежнему относительно велика.
«По данным о продажах baosteel, на собственные бренды Китая приходилось 41% потребления высокопрочной стали в 2017 году, и было продано более 28 миллионов европейских, японских, американских и корейских собственных автомобилей. Материалы, предоставляемые baosteel, относительно высокого качества, и наш средний национальный уровень будет немного ниже этого уровня. Коэффициент применения высокопрочной стали достигает в среднем 42-45% по нашим данным за прошлый год, что должно быть относительно низкий, а 60-70% за границей. Этот разрыв — наш потенциал».
Конкуренция междуалюминиевый листи стали, выдающимся преимуществом алюминия является низкая плотность и снижение массы тела в соответствии с пропорциейстали, необходимость утончения стального листа. В то время как обычные стальные листы обычно имеют толщину от 0,7 до 0,75 мм, сегодняшние сверхпрочные листы имеют толщину всего 0,65 мм или тоньше, а толщина капота нового Opel Seferli составляет 0,6 мм.
По словам Ван Ли, «если удельный вес стали не меняется, вес можно только уменьшить до более тонкого, а плотность можно отрегулировать. Теперь у нас есть новая идея, которая состоит в том, чтобы отрегулировать плотность стали. Преимуществом алюминия является низкая плотность, конкуренция в определенной степени. Я могу использовать ваши преимущества, чтобы отрегулировать мою плотность. Мы повысили модуль упругости стали. , и теперь он находится в лаборатории. Я хочу отметить, что, поскольку сама сталь остается неизменной на основе существующей промышленной промышленности, остается много места для инноваций. С этой точки зрения сталь по-прежнему сохраняет свою жизнеспособность, равно как и ее доля на рынке. Если автомобиль будет продаваться по цене более 200 000 юаней, он будет использовать больше материалов. Если автомобиль будет продаваться за 100 000 юаней, в нем все равно будет использоваться сталь».
Но проблема стоимости также становится другим материалом для замены основного положения корпуса из твердой стали. Шу-мин Чен сказал: «В соответствии с тенденцией облегчения веса автомобилей, хотя сейчас все делают легкие материалы, такие как алюминиевый сплав, магниевый сплав и другие. легкие композитные материалы, высокопрочная сталь или в основном положении тела, но я думаю, что основными факторами является стоимость, я считаю, что если стоимость углеродного волокна, вероятно, углеродное волокно заменит, это не невозможно, ключевая стоимость сейчас слишком высока, сталь в настоящее время также имеет очень большое преимущество в цене».
В дополнение к стоимости, в пределах диапазона прочности для удовлетворения спроса, хороший и простой процесс формования также становится причиной того, что сталь трудно заменить». С точки зрения развития, прочность стали для автомобиля не очень высокий. 1000 МПа достаточно. Высокопрочная сталь теперь в основном углеродистая для упрочнения, многие сделали 2200 МПа, но выше 2200 МПа произведут мутацию, или 2200-2500 МПа углерод упрочнить в принципе невозможно. другие материалы для замены углерода, прочность будет все выше и выше, но он не обязательно используется в автомобиле, он может использоваться в других областях с высокой прочностью. Для автомобилей у нас есть широкий выбор стали до 1000 МПа, низкая стоимость и очень хороший процесс формовки, так что какое-то время заменить сталь в нашей стране будет очень сложно».
И, судя по структурным свойствам самой стали, она хорошо ремонтируется. Чжу Цян указал, что сама по себе сталь с фазовым переходом имеет некоторые преимущества в некоторых применениях. «Для автомобильной стали, поскольку сталь имеет фазовые переходы, если она попадает в яму, его можно легко отремонтировать, что относительно сложно для композитов или алюминия. Например, композитный материал из алюминиевого сплава, если отверстие сломано, основной ремонт - это полная замена, стоимость также высока, это слабость сам алюминий по сравнению со сталью.
Алюминиевый сплавпериод развития встречался до волка после тигра
Цифры показывают, что для изготовления среднего автомобиля среднего размера требуется 725 кг стали и чугуна и 350 кг штампованной стали. Для сравнения, вес алюминия в европейском автомобиле увеличился с 50 кг в 1990 г. до 131,5 кг в 2005 г. большинство из них до сих пор используется во внутренних деталях двигателей и блоках цилиндров и растет. Алюминий также популярен в автомобилях, потому что он вдвое легче железа, материала, используемого для изготовления стали, и имеет лучшую коррозионную стойкость, чем сталь.
В настоящее время для изготовления кузова модели широко используется алюминиевый сплав. С момента своего рождения в 1994 году Audi A8 приняла полностью алюминиевую конструкцию кузова с пространственной рамой, а модель S разработана и изготовлена компанией tesla. также принимает полностью алюминиевый корпус. После запуска в производство полностью алюминиевой производственной линии Chery Jaguar Land Rover в Чаншу, провинция Цзянсу,первый отечественный автомобиль, новый уровень применения материала из алюминиевого сплава Jaguar XFL достиг 75%. Высокопрочный алюминиевый сплав nobelis RC5754, используемый во многих частях кузова Jaguar XFL, имеет предел текучести 105-145 МПа, предел прочности на растяжение 220 МПа. , а также хорошие показатели прочности, коррозионной стойкости, связности и скорости формования.
«Сейчас для автомобилей все больше используется алюминий, особенно для деталей шасси, помимо кузова, сейчас очень много автомобилей продолжают ходить по этой дороге. Есть некоторые проблемы с цельноалюминиевой рамой, но они прорабатываются. ». Чжан Хайтао, исследователь из Университета Сучжоу, сказал: «Зачем использовать полностью алюминиевые рамы? Во-первых, стоимость относительно низкая, стоимость небольшого автомобиля может составлять несколько тысяч юаней за раму, наиболее важным является конструкция сечения. очень сложный, а алюминий на изгиб и жесткость на кручение лучше, чем сталь.
Кроме того, алюминий имеет лучшее восстановление ресурсов и более длительный жизненный цикл, чем сталь. Чжу Цян сказал: «Уровень потерь при переработке алюминия составляет всего от 5 до 10 процентов. Если сталь заржавела, ее очень трудно восстановить. Алюминиевые сплавы имеют преимущества в долгосрочной перспективе. Если колеса с алюминием, теперь у нас есть консенсус в отношении того, что колеса из алюминиевого сплава должны быть лучше, чем сталь, потому что сталь легко ржавеет, соскабливание алюминиевого сплава не имеет значения, эта производительность стали не Для сравнения, характеристики композита из алюминиевого сплава в этом отношении имеют уникальное преимущество». Кроме того, длительный жизненный цикл также важен для автомобильной промышленности, и каждый продукт должен быть разработан с учетом длительного жизненного цикла. В этом отношении алюминий также имеет преимущество».
Чжу Цян также указал, что состав алюминиевого сплава относительно сложен, и переработка классификации также является проблемой». Например, для литья под давлением две пластины из сплава нельзя использовать вместе, они должны быть разделены, требуется много усилий, чтобы соединить их, и много усилий, чтобы их разделить. С одной стороны, эффективность восстановления невелика, а с другой стороны, ею непросто управлять. Кроме того, существует множество проблем, связанных с переработкой алюминия, таких как сокращение использования, можно использовать хорошую переработку алюминия. делать то, что не важно, то, что было бы хорошо, в конечном итоге имеет низкую ценность».
С точки зрения усталостных свойств материалов алюминий более опасен, чем сталь, а его обработка ограничена». Усталостные характеристики ключевых компонентов транспортных средств контролируются не только свойствами самих материалов, но и дефектами их деталей. материалы. Способность алюминия к окислению очень сильна, эти дефекты имеют относительно большое влияние на усталостные характеристики компонентов, очень легко пойти не так. Сталь не так сильно окисляется, и ее дефекты имеют относительно небольшое влияние на усталостные характеристики». Чжу Цян сказал: «Только с ковкой не может быть сложных компонентов, ковка должна быть обработана, иначе она не сможет удовлетворить потребности структурного дизайна. Вообще говоря, есть два вида ковки: либо отказ от структурной оптимизации, либо переработка. Однако, как только поверхность алюминиевого сплава повреждена, усталостные характеристики снизятся, а стоимость снова возрастет. Это проблемы, которые необходимо решить алюминиевым сплавам, и после решения этих проблем можно заменить сталь».
В автомобильном шасси алюминий заменил часть стали, но в последние годы, с развитием технологии стали, сталь шасси представила новые решения. Чжу Цян сказал: «Теперь шасси со сталью, мы разработали несколько технологий, одна из которых — это рычаг, теперь мы можем сделать стальной треугольный рычаг до 780 МПа, он менее чем на 10 процентов тяжелее алюминия, что намного дешевле. Между двумя колесами также есть связь, которая очень тяжелая, и теперь мы разработали новую технологию, которая уменьшает вес на 40 процентов и решает проблему коррозии с помощью покрытий, а стальсама улучшается. Теперь сталь и алюминий конкурируют друг с другом, поэтому у автомобильных компаний больше возможностей, а значит, и развития».
Фактически, современный автомобильный алюминий вышел на этап перед волком после тигра. Бывшие производители стали за счет постоянного улучшения характеристик, теперь сталь без никеля может добиться ржавчины, в то время как последний магниевый сплав, углеродное волокно и другие материалы с меньшими затратами и улучшенные характеристики оказали влияние на рынок алюминия. Чжу Цян отметил, что «алюминиевый сплав, чтобы преуспеть, может быть только быстрым развитием, потому что сталь делала так много лет, чтобы заменить ее трудно, алюминий должен быть индустриализирован как как можно скорее, не будет легко заменен позже, нынешние автомобильные алюминиевые проблемы и возможности сосуществуют.
Гибридная конструкция кузова из стали и алюминия — тренд
В настоящее время все больше и больше инженеров-автомобилестроителей уделяют больше внимания гибридному применению легких материалов. Их исследования и разработки сосредоточены не только на конкретном соотношении автомобильной стали и алюминия, но и на том, как правильно смешивать различные материалы. Инновации и модернизация конструкции кузова, заброшенные Audi всегда гордились всем алюминиевым корпусом, алюминиевым сплавом с наклоном до 58%, в дополнение к идентичности, в материале кузова добавлено больше композитных материалов, вес тела составляет почти 51 кг. тяжелее наличной модели, у наличной модели A8 236 кг «противоположный вес до 282 кг.
Новое поколение Audi A8 использует алюминиевый сплав для создания общей рамы кузова. Для обеспечения прочности конструкции в ключевых соединениях используются алюминиевые отливки, а на поверхности кузова используются детали из листового металла. В каркасной конструкции кузова используется большое количество сверхвысокопрочной легированной стали горячего формования, намного больше, чем в настоящее время. Высокопрочная сталь A8 только при применении колонны B, высокопрочного стального материала и 20 лет назад по сравнению со сталью, жесткость увеличилась в 5 раз, вес уменьшился на 40%. В структуру кузова добавлен магниевый сплав и углеродное волокно CFRP. в задней части автомобиля используется композитный материал, что снижает вес кузова от такой детали, как задняя панель.
«В будущем алюминий будет все больше использоваться во всем кузове автомобиля, и будет много гибридных кузовов. Например, алюминиевый кузов ауди А8 тоже начинают делать гибридные кузова, и теперь этому примеру следуют многие отечественные автопроизводители. Основная проблема соединений из стали и алюминия — коррозионная стойкость, на склейке, на тросе, без сварки. из стали, а нижняя часть кузова из алюминия. Например, оконная рама автомобиля Beijing сделана из стали сверху и алюминия снизу. Не то чтобы сталь была плоха, но я думаю, что более перспективно смешать сталь с алюминием. — сказал Чжан Хайтао.
В связи с этим Ван Ли также отметил, что на самом деле, еще в 1940-х годах, когда существовала конкуренция между сталью и алюминием, после многих лет развития автомобильные материалы достигли определенного консенсуса в отношении того, являются ли правильные материалы используемыми в нужном месте. .И сама сталь быстро развивается, как с конкуренцией, так и с сотрудничеством. И эта конкуренция более полезна для развития автомобильных предприятий, потому что существование конкуренции у автомобильных предприятий может иметь больше вариантов. Заглядывая в будущее, новые энергетические автомобили могут иметь более высокие Требования к легкости.
Стратегия «независимые бренды должны быть легкими, хорошая сталь с ее потенциалом все еще не мала, с помощью брендов совместного предприятия с долей высокопрочной стали и очень легко добиться 10% потери веса белого тела, за счет усилия другого транспортного средства падение 7% 8% возможно, тождестводоля передовых технологий может достичь тела без изменений более чем на 10%». «С некоторыми новыми технологиями и приемами можно добиться потери веса более чем на 20 процентов. Мы проанализировали многие модели наших собственных брендов, и потенциал по-прежнему велик. Разрыв - наша мотивация