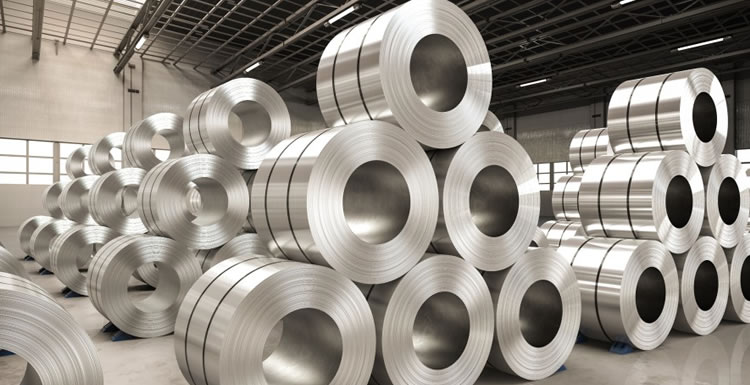
bobina din tablă de aluminiu concurează cu oțelul
Oțelul a fost întotdeauna principalul material în producția de automobile. Dar, odată cu protecția mediului și economisirea energiei din ce în ce mai ridicate, politica națională de consum de combustibil tinde să se înăsprească, consumatorii propun, de asemenea, cerințe mai mari pentru siguranța vehiculelor, ceea ce a forțat producătorii de automobile să căutați materiale de construcție pentru vehicule mai puternice și mai ușoare. Utilizarea oțelului de înaltă rezistență este de așteptat să ajungă la aproape 15% din greutatea vehiculului până în 2020, potrivit unui raport al centrului de cercetare auto. Până în 2040, această pondere va scădea treptat la aproape 5 la sută, când alte materiale ușoare vor avea un loc în afacerea cu materiale pentru automobile.
Cu mai puțin de jumătate din greutate și o rezistență la coroziune mai bună decât materia primă a oțelului, aluminiul a reprezentat cândva o amenințare pentru oțelul pentru automobile. Cu toate acestea, din cauza prețului relativ ridicat al aluminiului și a dificultății în procesele de fabricație și întreținere, mulți producători de automobile preferă să înlocuiți oțelul obișnuit cu oțel carbon de înaltă rezistență. Prin urmare, se joacă jocul dintre oțel și aluminiu. La forumul auto și de mediu desfășurat recent, experți din industrie, cum ar fi Wang Li, cercetător șef al institutului de cercetare Baosteel, zhu qiang, profesor catedr al Universității de Știință și Tehnologie din Sud, Chen shuming, profesor la Universitatea Jilin, Zhang Haitao și așa mai departe, a discutat despre „concurența din oțel și aluminiu” la masa rotundă.
Oțelul are un potențial mare de aplicare și un avantaj de cost
Odată cu dezvoltarea continuă a oțelului pentru automobile, oțelul pentru automobile este cu câteva decenii în urmă impresia multor oameni de oțel cu conținut scăzut de carbon, acum placa de oțel pentru automobile se subțiează, dar rezistența oțelului și rezistența la coroziune a fost mult îmbunătățită. Pentru a face față provocării noilor materiale, multe întreprinderi de producție de oțel dezvoltă în mod activ oțel ușor și de înaltă rezistență, care poate concura cu aliajul de aluminiu și alte materiale. Potrivit cifrelor, este nevoie de doar 212 euro de cost suplimentar per vehicul pentru oțel de înaltă rezistență pentru a obține pierderea în greutate și combustibil economii de aproximativ 5%.
Care este situația actuală și potențialul de aplicare al oțelului de înaltă rezistență pe piața auto din China? Wang li a analizat acest lucru, a spus că oțelul actual pentru automobile în eforturile continue de a reduce greutatea, „care a folosit o mulțime de tehnologie, una dintre cele contribuția este oțelul de înaltă rezistență. În ultimii 20 de ani, a existat un proiect iisa la care baosteel a participat. În cazul în care fabricile de oțel continuă să utilizeze oțel prin dezvoltarea de noi materiale, care este potențialul oțelului? Prin atât de mulți ani de dezvoltare, ultimul sfat sau tehnologie pentru fabrica auto, unul este de a dezvolta o varietate de oțel avansat de înaltă rezistență este încă pe drum, al doilea este de a dezvolta multe tehnologii avansate de fabricație și, în același timp, a introdus conceptul de ciclu de viață complet. De exemplu, cea mai recentă dezvoltare a unui concept de mașină electrică, reducerea greutății corporale de până la 40%, aceasta cu rezistență ridicată a oțelului este mai mare, mai mult de 1000 mpa de 40%, doar 5% este oțel moale, oțel prin puterea acestui potențial este încă relativ mare.
„Din datele de vânzări ale baosteel, mărcile proprii ale Chinei au reprezentat 41% din consumul de oțel de înaltă rezistență în 2017 și au fost vândute peste 28 de milioane de mașini proprii europene, japoneze, americane și coreene. Materialele furnizate de baosteel sunt relativ de calitate, iar nivelul nostru mediu național va fi puțin mai mic decât acest nivel. Rata de aplicare a oțelului de înaltă rezistență atinge o medie de 42-45% din datele noastre de anul trecut, care ar trebui să fie relativ scăzut, iar 60-70% în străinătate. Acest decalaj este potențialul nostru.”
Concurenţa dintretabla de aluminiuși oțel, avantajul remarcabil al aluminiului este densitatea scăzută și pentru a obține reducerea greutății corporale, în conformitate cu proporțiade oțel, necesitatea de a subțire placa de oțel. În timp ce foile de oțel obișnuite au, de obicei, o grosime cuprinsă între 0,7 și 0,75 mm, tablele super-rezistente de astăzi sunt de numai 0,65 mm sau mai subțiri, iar capota noului opel seferli are o grosime de 0,6 mm.
Potrivit lui Wang Li, „dacă greutatea specifică a oțelului nu este modificată, greutatea poate fi redusă doar la mai subțire, dar densitatea poate fi ajustată. Acum avem o nouă idee de făcut, și anume să reglam densitatea oțelului. Avantajul aluminiului este densitatea scăzută, concurența într-o anumită măsură. Pot folosi avantajele tale pentru a-mi ajusta densitatea. Am crescut modulul elastic al oțelului. , iar acum este în laborator. Un punct pe care vreau să-l subliniez este că, deoarece oțelul în sine rămâne neschimbat pe baza industriei industriale existente, există încă mult loc pentru inovare. Din această perspectivă, oțelul are încă o oarecare vitalitate, precum și cota de piață. Dacă mașina se vinde cu mai mult de 200.000 de yuani, va folosi mai multe materiale. Dacă mașina se vinde cu 100.000 de yuani, va folosi în continuare oțel.”
Dar problema costurilor devine, de asemenea, un alt material pentru a înlocui poziția principală a corpului de oțel motiv dur. Shu-ming Chen a spus, „sub tendința de ușurare auto, deși acum toată lumea face materiale ușoare, cum ar fi aliaj de aluminiu, aliaj de magneziu și alte materiale compozite ușoare, oțel de înaltă rezistență sau în poziția principală a corpului, dar cred că principalii factori sunt costul, cred că, dacă costul fibrei de carbon, fibra de carbon va înlocui probabil, nu este imposibil, cheia acum costul este prea mare, oțelul are în prezent și un avantaj foarte mare de cost.”
Pe lângă cost, în intervalul de rezistență pentru a satisface cererea, procesul de formare bun și ușor devine și motivul pentru care oțelul este dificil de înlocuit.” Din punct de vedere al dezvoltării, rezistența oțelului pentru mașină este nu foarte mare. 1000 mpa este suficient. Oțelul de înaltă rezistență este acum în principal carbon pentru a consolida, mulți au făcut 2200 mpa, dar peste 2200 mpa, va produce o mutație, sau 2200-2500 mpa carbon pentru a întări practic imposibil.” Cred că acest oțel va avea cu siguranță alte materiale pentru a înlocui carbonul, rezistența va fi din ce în ce mai mare, dar nu este neapărat folosit în mașină, poate fi folosit în alte zone cu rezistență ridicată. Pentru mașini, avem o selecție largă de oțel sub 1000 mpa, scăzut cost și proces de formare foarte bun, așa că va fi foarte dificil să înlocuim oțelul în țara noastră pentru o perioadă.”
Și din proprietățile structurale ale oțelului însuși, are o reparație bună. Zhu qiang a subliniat că oțelul însuși cu tranziție de fază are unele avantaje în unele aplicații.” Pentru oțelul pentru automobile, deoarece oțelul are tranziții de fază, dacă lovește o groapă, poate fi reparat cu ușurință, ceea ce este relativ dificil pentru compozite sau aluminiu. De exemplu, materialul compozit din aliaj de aluminiu, dacă o gaură este spartă, reparația de bază este o piesă întreagă de înlocuire, costul este, de asemenea, mare, aceasta este slăbiciunea aluminiul în sine în comparație cu oțelul.
Aliaj de aluminiuperioada de dezvoltare întâlnită înaintea Lupului după tigru
Cifrele arată că este nevoie de 725 de kilograme de oțel și fontă și 350 de kilograme de oțel ștanțat pentru a face o mașină medie de dimensiune medie. În schimb, greutatea aluminiului într-o mașină europeană a crescut de la 50 kg în 1990 la 131,5 kg în 2005, cu cele mai utilizate încă în interiorul motorului și blocuri de cilindri și în creștere. Aluminiul este, de asemenea, popular în mașini, deoarece are mai puțin de jumătate din greutatea fierului, materialul folosit pentru a face oțel, și are o rezistență la coroziune mai bună decât oțelul.
În prezent, utilizarea aliajului de aluminiu pentru a face corpul modelului a fost o mulțime de. De la nașterea sa în 1994, Audi A8 a adoptat structura de caroserie din aluminiu, iar modelul S dezvoltat și fabricat de Tesla. adoptă, de asemenea, caroseria din aluminiu. După linia de producție din aluminiu a chery jaguar land rover din changshu, provincia Jiangsu a fost pusă în producție,prima mașină autohtonă, noul Jaguar XFL, rata de aplicare a materialului din aliaj de aluminiu a ajuns la 75%. Aliajul de aluminiu de înaltă rezistență nobelis RC5754 utilizat în multe dintre părțile caroseriei Jaguar XFL are un randament de 105-145 Mpa, o rezistență la tracțiune de 220 Mpa. , și o performanță bună în rezistență, rezistență la coroziune, conectivitate și rata de turnare.
„Acum se folosește din ce în ce mai mult aluminiu pentru mașini, în special pentru piesele de șasiu, pe lângă caroserie, acum o mulțime de mașini continuă să meargă pe acest drum. Există unele probleme cu cadrul integral din aluminiu, dar sunt în curs de rezolvare. .” Zhang Haitao, un cercetător la Universitatea Soochow, a spus: „De ce să folosiți cadre din aluminiu? Primul cost este relativ scăzut, costul unei mașini mici poate fi de câteva mii de yuani pe cadru, cel mai important este designul secțiunii. este foarte complex, iar rigiditatea la încovoiere și la torsiune a aluminiului este mai bună decât oțelul.
În plus, aluminiul are o recuperare mai bună a resurselor și un ciclu de viață mai lung decât oțelul. Dacă oțelul este ruginit, este foarte greu de recuperat. Aliajele de aluminiu au avantaje pe termen lung. Dacă roțile cu aluminiu, acum avem un consens că jantele din aliaj de aluminiu trebuie să fie mai bune decât oțelul, deoarece oțelul este ușor de atins rugina, răzuirea aliajului de aluminiu nu contează, acest oțel de performanță nu este Un mod de comparare, performanța compozitelor din aliaj de aluminiu în acest sens are un avantaj unic.” În plus, ciclul lung de viață este important și pentru industria auto și fiecare produs trebuie proiectat având în vedere ciclul de viață lung. De asemenea, aluminiul are un avantaj în acest sens.”
Zhu qiang a subliniat, de asemenea, că compoziția aliajului de aluminiu este relativ complexă, modul de reciclare a clasificării este, de asemenea, o problemă.” De exemplu, pentru cadrul de turnare sub presiune, cele două plăci de aliaj nu pot fi utilizate împreună, trebuie să fie separate, este nevoie de mult efort pentru a le conecta și este nevoie de mult efort pentru a le separa. Pe de o parte, eficiența de recuperare nu este mare și, pe de altă parte, nu este ușor de gestionat. În plus, există o mulțime de probleme implicate în reciclarea aluminiului, cum ar fi utilizarea redusă, reciclarea bună a aluminiului poate fi utilizată. pentru a face ceva care nu este important, ceea ce ar fi fost lucruri bune ajung la o valoare scăzută.”
În ceea ce privește proprietățile la oboseală ale materialelor, aluminiul este mai riscant decât oțelul, iar prelucrarea este limitată.” Performanța la oboseală a componentelor cheie ale vehiculelor este controlată nu numai de proprietățile materialelor în sine, ci și de defectele acestora. materiale.Capacitatea de oxidare a aluminiului este foarte puternică, aceste defecte au un impact relativ mare asupra performanței la oboseală a componentelor, foarte ușor de greșit.Oțelul nu se oxidează atât de mult, iar defectele sale au un impact relativ scăzut asupra performanței la oboseală.” Zhu qiang a spus, „numai cu forjare nu pot fi componente complexe, forjarea trebuie procesată, altfel nu poate satisface nevoile de proiectare structurală. În general, există două tipuri de forjare, fie renunțând la optimizarea structurală, fie la reprocesare. Cu toate acestea, odată ce suprafața aliajului de aluminiu este deteriorată, performanța la oboseală va scădea, iar costul va crește din nou. Acestea sunt problemele pe care aliajele de aluminiu trebuie să le depășească și este posibil să înlocuiți oțelul după rezolvarea acestor probleme.”
În șasiul auto, aluminiul a înlocuit o parte din oțel, dar în ultimii ani, odată cu dezvoltarea tehnologiei oțelului, oțelul șasiului a introdus noi soluții. Zhu qiang a spus: „acum șasiu cu oțel, am dezvoltat mai multe tehnologii, una este brațul, acum la 780 mpa putem face acum braț triunghiular din oțel, este cu mai puțin de 10 la sută mai greu decât aluminiu, cost mult mai mic. Există, de asemenea, o legătură între cele două roți care este foarte grea, iar acum am dezvoltat o nouă tehnologie care reduce greutatea cu 40 la sută și rezolvă problema coroziunii prin folosirea de acoperiri și oțelîn sine se îmbunătățește. Acum oțelul și aluminiul concurează pentru a se promova unul pe celălalt, așa că există mai multe opțiuni pentru companiile auto și, prin urmare, pentru dezvoltare.”
De fapt, actualul aluminiu auto a intrat în faza înainte de Lup după tigru. Fostii producători de oțel prin îmbunătățirea continuă a performanței, acum oțel fără nichel poate obține rugina, în timp ce acesta din urmă aliaj de magneziu, fibră de carbon și alte materiale cu costuri mai mici și performanță îmbunătățită, au format un impact asupra pieței de aluminiu. Zhu qiang a subliniat, „aliaj de aluminiu pentru a face bine poate fi doar o dezvoltare rapidă, deoarece oțelul a făcut de atât de mulți ani pentru a înlocui este dificil, aluminiu trebuie să fie industrializare ca cât mai curând posibil, nu va fi înlocuit cu ușurință de mai târziu, provocările și oportunitățile actuale din aluminiu auto coexistă.
Structura caroseriei hibridă oțel – aluminiu este tendința
În prezent, din ce în ce mai mulți ingineri din producția de automobile acordă mai multă atenție aplicării hibride a materialelor ușoare. Accentul lor de cercetare și dezvoltare nu se pune doar pe raportul specific dintre oțel și aluminiu pentru automobile, ci și pe modul de amestecare corect a diferitelor materiale. Anul trecut, debutul la Salonul auto de la Frankfurt la noul Audi A8 a fost de tipul cadru spațial din aluminiu al Audi. Tehnologia structurii caroseriei inovație și upgrade, a abandonat Audi a fost întotdeauna mândru de întregul corp de aluminiu, aliaj de aluminiu de pantă la 58%, în plus față de identitatea, în materialul corpului adăugat mai multe materiale compozite, corpul este de aproape 51 kilograme mai greu decât modelul cash, de modelele cash A8 de 236 kg „greutate contrară la 282 kg.
Noua generație de Audi A8 adoptă aliaj de aluminiu pentru a construi cadrul general al caroseriei. Pentru a asigura rezistența structurală, piese turnate din aluminiu sunt utilizate în îmbinările cheie și părțile din tablă sunt utilizate pe suprafața corpului. În structura cuștii cabinei a caroseriei, un număr mare de oțel aliat de înaltă rezistență formare la cald, mult mai mult decât actualul Oțel de înaltă rezistență A8 numai în aplicarea coloanei B, materialul din oțel de înaltă rezistență și acum 20 de ani în comparație cu oțel, rigiditatea a crescut de 5 ori, greutatea redusă cu 40%. La structura corpului se adaugă aliaj de magneziu și fibră de carbon CFRP materialul compozit este utilizat în partea din spate a mașinii, ceea ce reduce greutatea caroseriei de la detalii precum panoul din spate.
„În viitor, aluminiul va fi folosit din ce în ce mai mult în toată caroseria mașinii și vor exista o mulțime de caroserii hibride. De exemplu, caroseria din aluminiu audi A8 începe să facă și caroserii hibride, iar acum multe companii auto autohtone urmează exemplul. Principala problemă a conexiunilor din oțel și aluminiu este rezistența la coroziune, cu lipire, cu ataș, fără sudură. Corpul superior este realizat. din oțel, iar corpul inferior este din aluminiu. De exemplu, cadrul ferestrei automobilului Beijing este din oțel deasupra și aluminiu în partea de jos. Nu că oțelul este rău, dar cred că este mai promițător să amesteci oțel cu aluminiu. ” a spus Zhang Haitao.
În acest sens, Wang Li a subliniat, de asemenea, că, de fapt, încă din anii 1940, când a existat o competiție pentru oțel și aluminiu, după mulți ani de dezvoltare, acum materialele auto au ajuns la un oarecare consens, sunt materialele potrivite utilizate la locul potrivit. .Și oțelul în sine se dezvoltă rapid, atât cu concurență, cât și prin cooperare. Și această competiție este mai benefică pentru dezvoltarea întreprinderilor de automobile, deoarece existența întreprinderilor de automobile concurente poate avea mai multe opțiuni. Privind în viitor, vehiculele cu energie nouă pot avea mai multe cerințe pentru greutatea ușoară.
Strategia „mărcilor independente trebuie să fie ușoară, oțelul bun cu potențialul său nu este încă mic, prin intermediul mărcilor în joint venture cu proporția de oțel de înaltă rezistență și este foarte ușor să se realizeze 10% din pierderea în greutate corporală albă, prin intermediul eforturile altor vehicule scădere 7% 8% este fezabilă, identitateadin proporția tehnologiei avansate se poate realiza corp fără schimbare de mai mult de 10%.” „Cu unele tehnologii și tehnici noi, se poate obține o pierdere în greutate de peste 20 la sută. Am analizat multe modele ale mărcilor proprii și potențialul este încă grozav. Decalajul este motivația noastră