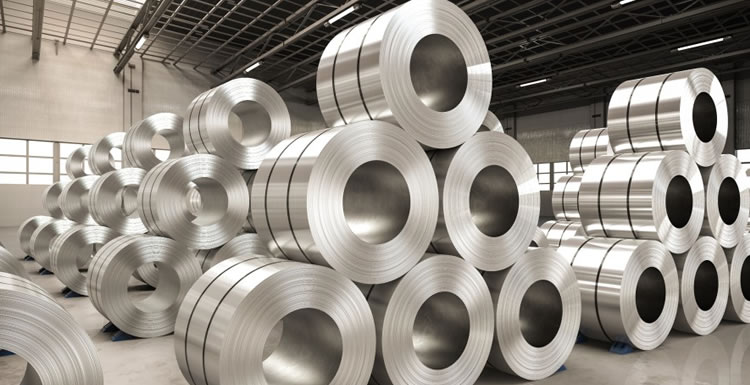
일반 강판의 두께가 보통 0.7~0.75mm인 데 비해 오늘날 초강력 강판은 0.65mm 이하에 불과하며 신형 오펠 세페를리의 보닛은 두께가 0.6mm에 불과하다.
왕리에 따르면 “강철의 비중이 변하지 않는다면 무게는 가늘어질 수 밖에 없고 밀도는 조절할 수 있다. 이제 우리는 강철의 밀도를 조정하는 새로운 아이디어를 얻었습니다. 알루미늄의 장점은 밀도가 낮다는 것입니다. 어느 정도 경쟁은 내 밀도를 조정하기 위해 당신의 장점을 사용할 수 있습니다. 우리는 강철의 탄성 계수를 높였습니다. , 그리고 지금은 연구실에 있습니다. 제가 말하고 싶은 한 가지는 철강 자체가 기존 산업 산업을 기반으로 하여 변함이 없기 때문에 여전히 혁신의 여지가 많다는 것입니다. 이러한 관점에서 볼 때 철강은 시장 점유율과 마찬가지로 여전히 약간의 활력을 가지고 있습니다. 자동차가 20만 위안 이상에 판매되면 더 많은 재료를 사용하게 됩니다. 자동차가 10만 위안에 팔리더라도 여전히 강철을 사용할 것입니다.”
그러나 비용 문제는 또한 강철의 본체 위치를 대체하는 다른 재료가 되는 어려운 이유가 됩니다. Shu-ming Chen은 다음과 같이 말했습니다. 경량 복합 재료, 고강도 강철 또는 본체 위치에 있지만 주요 요인은 비용이라고 생각합니다. 탄소 섬유의 비용이 탄소 섬유로 대체될 가능성이 있다고 생각합니다. 불가능하지는 않습니다. 이제 핵심은 비용입니다. 너무 높으면 현재 철강도 매우 큰 비용 이점을 가지고 있습니다."
비용과 더불어 수요에 부응할 수 있는 강도 범위 내에서 가공이 용이하고 좋은 철강재를 대체하기 어려운 이유도 된다.” 개발 관점에서 보면 자동차용 철강의 강도는 그다지 높지 않습니다. 1000 mpa면 충분합니다. 고강도 강철은 이제 주로 탄소로 강화되어 많은 사람들이 2200 mpa를 수행했지만 2200 mpa 이상에서는 돌연변이가 발생하거나 2200-2500 mpa 탄소를 강화하여 기본적으로 불가능합니다." 탄소를 대체할 다른 재료는 강도가 점점 더 높아지겠지만 자동차에 반드시 사용되는 것은 아니며 다른 고강도 영역에도 사용될 수 있습니다. 자동차의 경우 1000mpa 미만, 낮은 비용과 성형 공정이 매우 우수하여 당분간 우리나라에서 철강을 대체하기가 매우 어려울 것입니다.”
그리고 강철 자체의 구조적 특성으로 인해 수리가 잘됩니다. Zhu qiang는 상전이가 있는 강철 자체가 일부 응용 분야에서 몇 가지 장점이 있다고 지적했습니다. 그것은 쉽게 수리 할 수 있습니다. 이는 복합 재료 또는 알루미늄에 비해 상대적으로 어렵습니다. 예를 들어 알루미늄 합금 복합 재료는 구멍이 파손되면 기본 수리가 전체 교체 부품이며 비용도 높기 때문에 이것이 약점입니다. 강철에 비해 알루미늄 자체.
알루미늄 합금
호랑이 이후 늑대 이전에 만난 발달 기간
수치에 따르면 평균적인 중형차를 만드는 데 725kg의 강철과 주철, 350kg의 스탬프 강철이 필요합니다. 대조적으로 유럽 자동차의 알루미늄 무게는 1990년 50kg에서 2005년 131.5kg으로 증가했습니다. 여전히 엔진 내부 및 실린더 블록에 가장 많이 사용되며 상승합니다. 알루미늄은 강철을 만드는 재료인 철의 무게의 절반 미만이며 강철보다 내식성이 우수하기 때문에 자동차에서도 인기가 있습니다.현재 모델의 바디를 만들기 위해 알루미늄 합금을 많이 사용하고 있습니다. 1994년 출시된 이후로 audi A8은 전체 알루미늄 스페이스 프레임 바디 구조를 채택했고, Model S는 테슬라에서 개발 및 제조되었습니다. 또한 모든 알루미늄 바디를 채택합니다. 장쑤성 창수에 있는 체리 재규어 랜드로버의 전체 알루미늄 생산 라인이 생산에 들어간 후,자체적으로 개선되고 있습니다. 이제 철강과 알루미늄은 서로를 홍보하기 위해 경쟁하므로 자동차 회사에 더 많은 옵션이 있고 따라서 개발이 가능합니다.”실제로 현재의 자동차 알루미늄은 호랑이를 따라 늑대보다 앞선 단계에 진입했습니다. 이전 철강 제조업체는 성능의 지속적인 개선을 통해 이제 니켈이 없는 철강은 녹을 얻을 수 있고 후자는 마그네슘 합금, 탄소 섬유 및 기타 재료를 저렴한 비용으로 얻을 수 있습니다. 및 개선된 성능은 알루미늄 시장에 영향을 미쳤습니다. Zhu qiang는 "강철이 수년 동안 이를 대체하는 것이 어렵기 때문에 알루미늄 합금은 빠르게 발전할 수 있습니다. 알루미늄은 산업화해야 합니다. 가능한 한 빨리, 나중으로 쉽게 대체되지 않을 것이며, 현재의 자동차 알루미늄 문제와 기회가 공존하고 있습니다.
스틸 – 알루미늄 하이브리드 차체 구조가 대세
현재 점점 더 많은 자동차 제조 엔지니어가 경량 재료의 하이브리드 적용에 더 많은 관심을 기울이고 있습니다. 그들의 연구 개발 초점은 자동차 강철과 알루미늄의 특정 비율뿐만 아니라 다양한 재료를 올바르게 혼합하는 방법에 있습니다. 작년 프랑크푸르트 모터쇼에서 새로운 audi A8에서 데뷔는 audi의 알루미늄 스페이스 프레임 유형이었습니다. 차체 구조 기술 혁신 및 업그레이드, 버려진 아우디는 항상 전체 알루미늄 차체, 58%까지 경사의 알루미늄 합금을 자랑스럽게 생각하며, 정체성 외에도 차체 재료에 더 많은 복합 재료를 추가했으며 본체는 거의 51kg입니다. 현금 모델보다 무거운, 236kg의 현금 A8 모델에 의해 "반대 무게 282kg.
새로운 세대의 audi A8은 알루미늄 합금을 채택하여 차체의 전체 프레임을 구성합니다. 구조적 강도를 보장하기 위해 주요 조인트에는 알루미늄 주물이 사용되고 차체 표면에는 판금 부품이 사용됩니다. 차체의 캐빈 케이지 구조에서는 현재보다 훨씬 많은 열간 성형 초고강도 합금강이 사용됩니다. A8고장력강은 B컬럼만 적용한 고강도 강재로 20년 전 강재에 비해 강성은 5배 증가, 무게는 40% 감소했다. 차체 구조에 마그네슘 합금이 추가됐으며, CFRP 탄소섬유 자동차 후면에는 복합 소재를 사용하여 후면 패널과 같은 세부 사항에서 차체 무게를 줄입니다.
“앞으로 알루미늄은 차체 전체에 점점 더 많이 사용될 것이고, 하이브리드 바디도 많이 나올 것입니다. 예를 들어, audi A8 알루미늄 바디도 하이브리드 바디를 만들기 시작했고 현재 많은 국내 자동차 회사가 이를 따르고 있습니다. 강철 및 알루미늄 연결의 주요 문제는 용접 없이 접착, 테더 포함, 내식성입니다. 예를 들어 북경 자동차의 창틀은 위가 철, 아래가 알루미늄입니다. 그 철이 나쁘다는 것은 아니지만, 철에 알루미늄을 섞는 것이 더 유망하다고 생각합니다. "장하이타오가 말했다.
이와 관련하여 왕리는 사실 1940년대 초반에는 철강과 알루미늄 경쟁이 있었고 수년간의 개발 끝에 이제는 자동차 재료가 어느 정도 합의에 이르렀고 올바른 장소에 올바른 재료가 사용되었다고 지적했습니다. . 그리고 철강 자체는 경쟁과 협력으로 빠르게 발전하고 있습니다. 그리고 이 경쟁은 자동차 기업의 발전에 더 유리합니다. 경쟁이 존재하면 자동차 기업이 더 많은 선택을 할 수 있기 때문입니다. 미래를 내다보면 신에너지 자동차는 더 높은 경량에 대한 요구 사항."독립 브랜드는 경량이어야하며 잠재력이 좋은 강철은 여전히 작지 않습니다. 고강도 강철의 비율이있는 합작 브랜드를 통해 백체 체중 감소의 10 %를 달성하는 것은 매우 쉽습니다. 다른 차량의 노력 드랍 7% 8% 가능, 아이덴티티선진 기술의 비율은 10% 이상의 변화 없이 신체를 달성할 수 있습니다."" 일부 새로운 기술과 기술로 20% 이상의 체중 감량을 달성할 수 있습니다. 우리는 우리 자신의 브랜드의 많은 모델을 분석했으며 잠재력 여전히 훌륭합니다. 격차는 우리의 동기