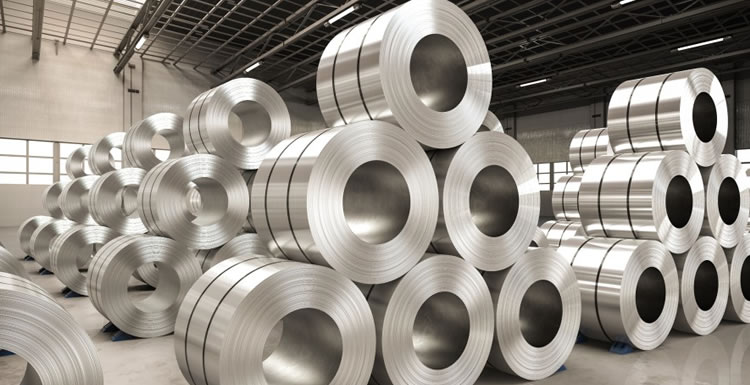
di acciaio, la necessità di assottigliare la piastra in acciaio. Mentre le lamiere di acciaio ordinarie hanno solitamente uno spessore compreso tra 0,7 e 0,75 mm, le lamiere super resistenti di oggi sono solo 0,65 mm o più sottili e il cofano della nuova opel seferli ha uno spessore di 0,6 mm.
Secondo wang li, "se il peso specifico dell'acciaio non viene modificato, il peso può essere ridotto solo a più sottile, ma la densità può essere regolata. Ora abbiamo una nuova idea da fare, che è regolare la densità dell'acciaio. Il vantaggio dell'alluminio è la bassa densità, la concorrenza in una certa misura posso usare i tuoi vantaggi per regolare la mia densità. Abbiamo aumentato il modulo elastico dell'acciaio , e ora è in laboratorio. Un punto che voglio sottolineare è che, poiché l'acciaio stesso rimane invariato sulla base dell'industria industriale esistente, c'è ancora molto spazio per l'innovazione. Da questo punto di vista, l'acciaio ha ancora una certa vitalità, così come la sua quota di mercato. Se l'auto venderà per più di 200.000 yuan, utilizzerà più materiali. Se l'auto viene venduta a 100.000 yuan, utilizzerà comunque l'acciaio".
Ma il problema dei costi diventa anche altro materiale per sostituire la posizione del corpo principale della ragione in acciaio duro. Shu-ming Chen ha detto, "sotto la tendenza dell'alleggerimento automobilistico, sebbene ora tutti facciano materiali leggeri, come leghe di alluminio, leghe di magnesio e altri materiali compositi leggeri, acciaio ad alta resistenza o nella posizione del corpo principale, ma penso che il fattore principale sia il costo, credo che se il costo della fibra di carbonio, la fibra di carbonio sostituirà il probabile, non è impossibile, la chiave ora è il costo troppo alto, l'acciaio attualmente presenta anche un notevole vantaggio in termini di costi".
Oltre al costo, all'interno della gamma di resistenza per soddisfare la domanda, il processo di formatura buono e facile diventa anche il motivo per cui l'acciaio è difficile da sostituire. "Dal punto di vista dello sviluppo, la resistenza dell'acciaio per l'auto è non molto alto. 1000 mpa sono sufficienti. L'acciaio ad alta resistenza ora è principalmente carbonio per rafforzare, molti hanno fatto 2200 mpa, ma al di sopra di 2200 mpa produrrà una mutazione, o 2200-2500 mpa di carbonio per rafforzare praticamente impossibile. "Credo che questo acciaio avrà sicuramente altri materiali per sostituire il carbonio, la resistenza sarà sempre più alta, ma non è necessariamente utilizzato nell'auto, può essere utilizzato in altre aree ad alta resistenza. Per le auto, abbiamo un'ampia selezione di acciaio inferiore a 1000 mpa, basso costo e un ottimo processo di formatura, quindi sarà molto difficile sostituire l'acciaio nel nostro paese per un po'".
E dalle proprietà strutturali dell'acciaio stesso, ha una buona riparazione. Zhu qiang ha sottolineato che l'acciaio stesso con transizione di fase presenta alcuni vantaggi in alcune applicazioni. "Per l'acciaio automobilistico, poiché l'acciaio ha transizioni di fase, se colpisce una fossa, può essere facilmente riparato, il che è relativamente difficile per compositi o alluminio. Ad esempio, materiale composito in lega di alluminio, se un foro è rotto, la riparazione di base è un intero pezzo di sostituzione, anche il costo è elevato, questa è la debolezza di alluminio stesso rispetto all'acciaio.
Lega di alluminio
periodo di sviluppo incontrato prima del lupo dopo la tigre
Le cifre mostrano che occorrono 725 chilogrammi di acciaio e ghisa e 350 chilogrammi di acciaio stampato per realizzare un'auto di medie dimensioni. Al contrario, il peso dell'alluminio in un'auto europea è aumentato da 50 kg nel 1990 a 131,5 kg nel 2005, con la maggior parte è ancora utilizzata negli interni del motore e nei blocchi cilindri e in aumento. L'alluminio è anche popolare nelle automobili perché pesa meno della metà del ferro, il materiale utilizzato per produrre l'acciaio, e ha una migliore resistenza alla corrosione dell'acciaio.Al momento, l'uso della lega di alluminio per realizzare la carrozzeria del modello è stato molto diffuso. Sin dalla sua nascita nel 1994, l'audi A8 ha adottato la struttura della carrozzeria interamente in alluminio space frame e la Model S sviluppata e prodotta da tesla adotta anche il corpo interamente in alluminio. Dopo che la linea di produzione interamente in alluminio di chery jaguar land rover a changshu, è stata messa in produzione la provincia di jiangsu,la prima auto domestica, il nuovo tasso di applicazione del materiale in lega di alluminio jaguar XFL ha raggiunto il 75%. La lega di alluminio ad alta resistenza nobelis RC5754 utilizzata in molte parti del corpo della jaguar XFL ha una resa di 105-145 Mpa, una resistenza alla trazione di 220 Mpa e una buona prestazione in termini di resistenza, resistenza alla corrosione, connettività e velocità di stampaggio."Ora si usa sempre più alluminio per le auto, soprattutto per le parti del telaio, oltre alla carrozzeria, ora molte auto continuano a percorrere questa strada. Ci sono alcuni problemi con il telaio interamente in alluminio, ma sono in fase di elaborazione "Zhang haitao, ricercatore presso l'università di Soochow, ha detto, "perché usare telai interamente in alluminio? Il primo costo è relativamente basso, il costo di una piccola auto può essere di qualche migliaio di yuan per telaio, il più importante è il design della sezione è molto complesso e la flessione dell'alluminio e la rigidità torsionale sono migliori dell'acciaio.
Inoltre, l'alluminio ha un migliore recupero delle risorse e un ciclo di vita più lungo rispetto all'acciaio. Zhu qiang ha affermato che "il tasso di perdita di riciclaggio dell'alluminio è solo del 5-10 percento. Se l'acciaio è arrugginito, è molto difficile da recuperare. Le leghe di alluminio hanno vantaggi a lungo termine. Se le ruote con alluminio, ora abbiamo un consenso sul fatto che i cerchi in lega di alluminio devono essere migliori dell'acciaio, perché l'acciaio è facile da toccare la ruggine, la raschiatura della lega di alluminio non ha importanza, questo acciaio ad alte prestazioni non lo è Per fare un confronto, le prestazioni dei compositi in lega di alluminio a questo riguardo hanno un vantaggio unico”. Inoltre, il lungo ciclo di vita è importante anche per l'industria automobilistica e ogni prodotto deve essere progettato tenendo presente il lungo ciclo di vita. Anche l'alluminio ha un vantaggio in questo senso".
Zhu qiang ha anche sottolineato che la composizione della lega di alluminio è relativamente complessa, anche come riciclare la classificazione è un problema. "Ad esempio, per la struttura della pressofusione, le due piastre di lega non possono essere utilizzate insieme, devono essere separati, ci vuole molto sforzo per collegarli e ci vuole molto sforzo per separarli. Da un lato, l'efficienza del recupero non è elevata e, dall'altro, non è facile da gestire. Inoltre, ci sono molti problemi coinvolti nel riciclaggio dell'alluminio, come un uso ridotto, può essere utilizzato un buon riciclaggio dell'alluminio per fare qualcosa che non è importante, quelle che sarebbero state cose buone finiscono con un valore basso”.
In termini di proprietà a fatica dei materiali, l'alluminio è più rischioso dell'acciaio e la lavorazione è limitata”. Le prestazioni a fatica dei componenti chiave dei veicoli sono controllate non solo dalle proprietà dei materiali stessi, ma anche dai difetti dei materiali. La capacità di ossidazione dell'alluminio è molto forte, questi difetti hanno un impatto relativamente grande sulle prestazioni a fatica dei componenti, molto facile sbagliare. L'acciaio non si ossida tanto e i suoi difetti hanno un impatto relativamente basso sulle prestazioni a fatica. "Zhu qiang ha detto, “solo con la forgiatura non possono essere componenti complessi, la forgiatura deve essere lavorata, altrimenti non può soddisfare le esigenze di progettazione strutturale. In generale, ci sono due tipi di forgiatura, o rinunciando all'ottimizzazione strutturale o rilavorazione. Tuttavia, una volta danneggiata la superficie della lega di alluminio, le prestazioni a fatica diminuiranno e il costo aumenterà di nuovo. Questi sono i problemi che le leghe di alluminio devono superare ed è possibile sostituire l'acciaio dopo aver risolto questi problemi".
Nel telaio automobilistico, l'alluminio ha sostituito parte dell'acciaio, ma negli ultimi anni con lo sviluppo della tecnologia dell'acciaio, l'acciaio del telaio ha introdotto nuove soluzioni. Zhu qiang ha detto: "ora telaio con acciaio, abbiamo sviluppato diverse tecnologie, una è il braccio, ora a 780 mpa ora possiamo fare il braccio a triangolo in acciaio, è meno del 10 percento più pesante dell'alluminio, un costo molto inferiore. C'è anche un collegamento tra le due ruote che è molto pesante e ora abbiamo sviluppato una nuova tecnologia che riduce il peso del 40 percento e risolve il problema della corrosione utilizzando i rivestimenti e l'acciaiosta migliorando. Ora l'acciaio e l'alluminio competono per promuoversi a vicenda, quindi ci sono più opzioni per le case automobilistiche, e quindi lo sviluppo".
Attualmente, sempre più ingegneri di produzione automobilistica prestano maggiore attenzione all'applicazione ibrida di materiali leggeri. Il loro focus di ricerca e sviluppo non è solo sul rapporto specifico tra acciaio e alluminio per autoveicoli, ma anche su come miscelare correttamente vari materiali. L'anno scorso al Salone di Francoforte il debutto della nuova Audi A8 è stato del tipo audi con telaio spaziale in alluminio. innovazione e aggiornamento della tecnologia della struttura del corpo, abbandonato l'audi è sempre stato orgoglioso dell'intero corpo in alluminio, lega di alluminio di pendenza al 58%, oltre all'identità di, nel materiale del corpo ha aggiunto più materiali compositi, il corpo è quasi 51 chilogrammo più pesante del modello cash, dai modelli cash A8 di 236 kg “peso contrario a 282 kg.
La nuova generazione di Audi A8 adotta la lega di alluminio per costruire il telaio complessivo della carrozzeria. Per garantire la resistenza strutturale, le fusioni di alluminio vengono utilizzate nei giunti chiave e le parti in lamiera vengono utilizzate sulla superficie del corpo. Nella struttura della gabbia della cabina del corpo, un gran numero di acciai legati ad altissima resistenza formati a caldo, molto più dell'attuale Acciaio ad alta resistenza A8 solo nell'applicazione della colonna B, il materiale in acciaio ad alta resistenza e 20 anni fa rispetto all'acciaio, rigidità aumentata 5 volte, peso ridotto del 40%. Alla struttura del corpo viene aggiunta una lega di magnesio e fibra di carbonio CFRP materiale composito è utilizzato nella parte posteriore dell'auto, che riduce il peso della carrozzeria da dettagli come il pannello posteriore.
“In futuro, l'alluminio sarà utilizzato sempre di più in tutta la carrozzeria e ci saranno molte carrozzerie ibride. Ad esempio, anche la carrozzeria in alluminio dell'audi A8 inizia a produrre carrozzerie ibride e ora molte case automobilistiche nazionali stanno seguendo l'esempio. Il problema principale con i collegamenti in acciaio e alluminio è la resistenza alla corrosione, con incollaggio, con cavo, senza saldatura. La parte superiore della carrozzeria è realizzata di acciaio e il corpo inferiore è in alluminio. Ad esempio, il telaio del finestrino dell'automobile di Pechino è in acciaio nella parte superiore e in alluminio nella parte inferiore. Non che l'acciaio sia cattivo, ma penso che sia più promettente mescolare l'acciaio con l'alluminio. "Ha detto Zhang Haitao.
A questo proposito, wang li ha anche sottolineato che in effetti già negli anni '40 quando c'era la concorrenza dell'acciaio e dell'alluminio, dopo molti anni di sviluppo, ora i materiali automobilistici hanno raggiunto un certo consenso, sono i materiali giusti usati al posto giusto E l'acciaio stesso si sta sviluppando rapidamente, sia con la concorrenza che con la cooperazione. E questa concorrenza è più vantaggiosa per lo sviluppo delle imprese automobilistiche, perché l'esistenza di imprese automobilistiche da competizione può avere più scelte. Guardando al futuro, i veicoli a nuova energia potrebbero avere una maggiore requisiti per il peso leggero.
La strategia dei "marchi indipendenti deve essere leggera, il buon acciaio con il suo potenziale non è ancora piccolo, per mezzo di marchi di joint venture con la proporzione di acciaio ad alta resistenza ed è molto facile ottenere il 10% della perdita di peso della pasta bianca, attraverso il gli sforzi di altri veicoli cadono 7% 8% è fattibile, l'identitàdella proporzione della tecnologia avanzata può raggiungere il corpo senza modifiche di oltre il 10%.""Con alcune nuove tecnologie e tecniche, è possibile ottenere una perdita di peso superiore al 20 percento. Abbiamo analizzato molti modelli dei nostri marchi e il potenziale è ancora fantastico. Il divario è la nostra motivazione