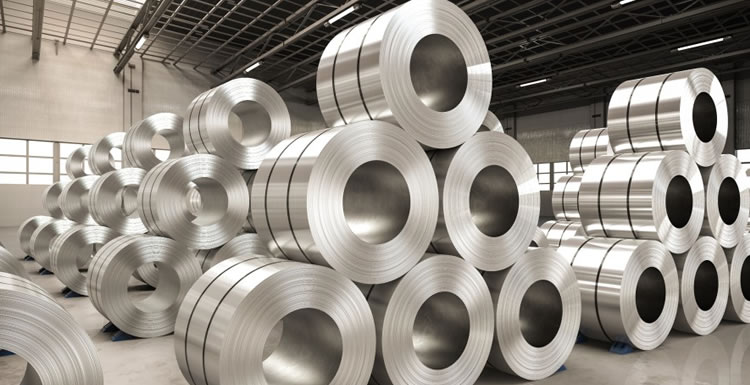
od čelika, potreba za stanjivanjem čelične ploče. Dok su obični čelični limovi obično debljine između 0,7 i 0,75 mm, današnji limovi super čvrstoće su samo 0,65 mm ili tanji, a poklopac motora novog Opel seferlija je debeo 0,6 mm.
Prema Wang Liju, “ako se specifična težina čelika ne promijeni, težina se može smanjiti samo na tanju, ali se gustoća može podesiti. Sada imamo novu ideju za napraviti, a to je prilagoditi gustoću čelika. Prednost aluminija je niska gustoća, konkurencija u određenoj mjeri mogu iskoristiti vaše prednosti da prilagodim svoju gustoću. Povisili smo modul elastičnosti čelika , a sada je u laboratoriju. Jedna stvar koju želim istaknuti je da, budući da sam čelik ostaje nepromijenjen na temelju postojeće industrijske industrije, još uvijek ima puno prostora za inovacije. Iz ove perspektive, čelik još uvijek ima određenu vitalnost, kao i svoj tržišni udio. Ako se automobil proda za više od 200.000 juana, koristit će više materijala. Ako se automobil proda za 100.000 juana, i dalje će koristiti čelik.”
No, problem troškova također postaje drugi materijal koji će zamijeniti glavni položaj tijela od čelika tvrdog razloga. Shu-ming Chen je rekao, „pod trendom automobilske lagane težine, iako sada svi rade lagane materijale, poput legure aluminija, legure magnezija i drugih lagani kompozitni materijali, čelik visoke čvrstoće ili u glavnom položaju tijela, ali mislim da je glavni čimbenik cijena, vjerujem da ako će cijena karbonskih vlakana, karbonska vlakna zamijeniti vjerojatno, to nije nemoguće, ključna cijena je sada previsoko, čelik trenutno također ima vrlo veliku prednost u troškovima.”
Osim cijene, unutar raspona čvrstoće kako bi se zadovoljila potražnja, dobar i jednostavan proces oblikovanja također postaje razlog zašto je čelik teško zamijeniti.” S razvojne točke gledišta, čvrstoća čelika za automobil je nije jako visoka. 1000 mpa je dovoljno. Čelik visoke čvrstoće je sada uglavnom ugljik za jačanje, mnogi su radili 2200 mpa, ali iznad 2200 mpa, proizvest će mutaciju, ili 2200-2500 mpa ugljika za jačanje u osnovi nemoguće.” Vjerujem da će ovaj čelik definitivno imati drugi materijali za zamjenu ugljika, čvrstoća će biti sve veća i veća, ali se ne koristi nužno u automobilu, može se koristiti u drugim područjima visoke čvrstoće. Za automobile imamo širok izbor čelika ispod 1000 mpa, niske trošak i vrlo dobar proces oblikovanja, tako da će kod nas neko vrijeme biti vrlo teško zamijeniti čelik.”
A što se tiče strukturnih svojstava samog čelika, ima dobar popravak. Zhu qiang je istaknuo da sam čelik s faznim prijelazom ima neke prednosti u nekim primjenama.” Za automobilski čelik, jer čelik ima fazne prijelaze, ako udari u jamu, može se lako popraviti, što je relativno teško za kompozite ili aluminij. Na primjer, kompozitni materijal od legure aluminija, ako je rupa slomljena, osnovni popravak je cijeli komad zamjene, trošak je također visok, to je slabost sam aluminij u usporedbi sa čelikom.
Aluminijska legura
razvojno razdoblje koje se susrelo prije Vuka nakon tigra
Brojke pokazuju da je za izradu prosječnog automobila srednje veličine potrebno 725 kilograma čelika i lijevanog željeza i 350 kilograma žigosanog čelika. Nasuprot tome, težina aluminija u europskom automobilu porasla je sa 50 kg 1990. na 131,5 kg 2005. većina se još uvijek koristi u unutrašnjosti motora i blokovima cilindara i raste. Aluminij je također popularan u automobilima jer je manje od polovice težine željeza, materijala koji se koristi za izradu čelika, i ima bolju otpornost na koroziju od čelika.Trenutačno se za izradu karoserije modela koristi aluminijska legura. Od svog rođenja 1994., audi A8 je usvojio potpuno aluminijsku strukturu svemirskog okvira, a model S razvila je i proizvela Tesla također usvaja potpuno aluminijsku karoseriju. Nakon potpuno aluminijske proizvodne linije chery jaguar land rover u changshuu, provincija jiangsu puštena je u proizvodnju,sama se poboljšava. Sada se čelik i aluminij natječu u promicanju jedni drugih, tako da postoji više opcija za automobilske tvrtke, a time i razvoj.”Zapravo, sadašnji automobilski aluminij je ušao u fazu prije Vuka nakon tigra. Bivši proizvođači čelika kroz kontinuirano poboljšanje performansi, sada čelik bez nikla može postići hrđu, dok drugi od legure magnezija, ugljičnih vlakana i drugih materijala s nižim troškovima i poboljšane performanse, utjecale su na tržište aluminija. Zhu qiang je istaknuo, „da bi aluminijska legura radila dobro, može se samo brzo razvijati, jer čelik je radio toliko godina kako bi ga zamijenio teško, aluminij mora biti industrijalizacija kao što je prije moguće, neće biti lako zamijeniti kasnije, trenutni automobilski aluminijski izazovi i prilike koegzistiraju.
Čelik – aluminij hibridna struktura karoserije je trend
Trenutno, sve više inženjera u proizvodnji automobila posvećuje više pažnje hibridnoj primjeni lakih materijala. Njihov fokus istraživanja i razvoja nije samo na specifičnom omjeru automobilskog čelika i aluminija, već i na tome kako pravilno miješati različite materijale. Prošle godine na sajmu automobila u Frankfurtu debi na novom audiju A8 bio je audijev aluminijski prostorni okvir. struktura karoserije tehnologija inovacija i nadogradnja, napušten audi je uvijek bio ponosan na cijelo aluminijsko tijelo, aluminijska legura nagiba do 58%, osim identiteta, u materijal karoserije dodano više kompozitnih materijala, tijelo je gotovo 51 kilogram teži od gotovinskog modela, kod gotovinskih A8 modela od 236 kg “suprotne težine do 282 kg.
Nova generacija Audija A8 koristi aluminijsku leguru za izgradnju cjelokupnog okvira karoserije. Kako bi se osigurala čvrstoća konstrukcije, aluminijski odljevci se koriste u ključnim spojevima, a dijelovi od lima se koriste na površini karoserije. U kaveznoj strukturi karoserije, veliki broj vruće oblikovanih legiranih čelika visoke čvrstoće, daleko više od trenutnog A8 čelik visoke čvrstoće samo u primjeni B stupca, čeličnog materijala visoke čvrstoće i prije 20 godina u usporedbi s čelikom, krutost je povećana 5 puta, težina smanjena za 40%. U strukturu karoserije dodana je legura magnezija, a ugljična vlakna CFRP U stražnjem dijelu automobila koristi se kompozitni materijal, koji smanjuje težinu karoserije od takvih detalja kao što je stražnja ploča.
“U budućnosti će se aluminij sve više koristiti u cijeloj karoseriji automobila, a bit će i puno hibridnih karoserija. Primjerice, aluminijska karoserija audi A8 počinje proizvoditi i hibridne karoserije, a sada to slijede mnoge domaće automobilske tvrtke. Glavni problem kod čeličnih i aluminijskih spojeva je otpornost na koroziju, s lijepljenjem, s vezom, bez zavarivanja. Gornji dio tijela je izrađen od čelika, a donji dio tijela izrađen je od aluminija. Na primjer, okvir prozora automobila u Pekingu je napravljen od čelika na vrhu i aluminija na dnu. Nije da je čelik loš, ali mislim da je više obećavajuće miješati čelik s aluminijem. “, rekao je Zhang haitao.
S tim u vezi, wang li je također istaknuo da je zapravo, već 1940-ih, kada je postojala konkurencija čelika i aluminija, nakon mnogo godina razvoja, sada su automobilski materijali postigli određeni konsenzus, pravi materijali koji se koriste na pravom mjestu .I sam čelik se brzo razvija, uz konkurenciju i suradnju. I ova konkurencija je korisnija za razvoj automobilskih poduzeća, jer postojanje konkurencije automobilska poduzeća mogu imati više izbora. Gledajući u budućnost, nova energetska vozila mogu imati više zahtjevi za laganu.Strategija „nezavisnih marki mora biti lagana, dobar čelik sa svojim potencijalom još uvijek nije mali, uz pomoć zajedničkih ulagača brendova s udjelom čelika visoke čvrstoće i vrlo je lako postići 10% gubitka tjelesne težine bijelog, kroz napori drugih vozila pad 7% 8% je izvedivo, identitetudjela napredne tehnologije može postići tijelo bez promjene od više od 10%.””S nekim novim tehnologijama i tehnikama može se postići više od 20 posto mršavljenja. Analizirali smo mnoge modele vlastitih marki, te potencijal još uvijek je super. Jaz je naša motivacija