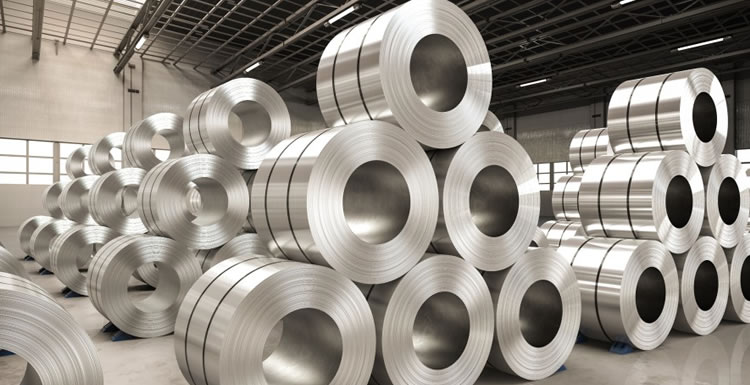
svitek hliníkového plechu konkuruje oceli
Ocel byla vždy hlavním materiálem ve výrobě automobilů. Ale se stále silnějším hlasem společnosti k ochraně životního prostředí a úsporám energie, národní politika spotřeby paliva má tendenci se zpřísňovat, spotřebitelé také kladou vyšší požadavky na bezpečnost vozidel, což donutilo výrobce automobilů hledejte pevnější a lehčí stavební materiály pro vozidla. Očekává se, že podle zprávy Centra pro automobilový výzkum do roku 2020 dosáhne používání vysokopevnostní oceli vrcholu téměř 15 procent hmotnosti vozidla. Do roku 2040 tento podíl postupně klesne na téměř 5 procent, když ostatní lehké materiály budou mít místo v byznysu s automobilovými materiály.
S méně než poloviční hmotností a lepší odolností proti korozi než surovina oceli, hliník kdysi představoval hrozbu pro automobilovou ocel. Nicméně kvůli relativně vysoké ceně hliníku a obtížnosti při výrobě a údržbě mnoho výrobců automobilů dává přednost nahradit běžnou ocel vysokopevnostní uhlíkovou ocelí. Proto se hraje hra mezi ocelí a hliníkem. Na automobilovém a ekologickém fóru, které se nedávno konalo, odborníci v tomto odvětví, jako je wang li, hlavní výzkumný pracovník výzkumného institutu baosteel, zhu qiang, profesor jižní univerzity vědy a technologie, Chen shuming, profesor univerzity v Jilin, zhang haitao a tak dále diskutovali u kulatého stolu o „soutěži oceli a hliníku“.
Ocel má velký aplikační potenciál a cenovou výhodu
S neustálým vývojem automobilové oceli není automobilová ocel před několika desetiletími vnímána mnoha lidmi jako nízkouhlíková ocel, nyní se automobilový ocelový plech ztenčuje, ale pevnost oceli a odolnost proti korozi se výrazně zlepšila. Aby bylo možné čelit výzvě nových materiálů, mnoho podniků vyrábějících ocel aktivně vyvíjí lehkou a vysokopevnostní ocel, která může konkurovat hliníkové slitině a dalším materiálům. Podle údajů je k dosažení úbytku hmotnosti a paliva zapotřebí pouze 212 eur na vozidlo navíc nákladů na vysokopevnostní ocel úspora cca 5 %.
Jaká je současná situace a aplikační potenciál vysokopevnostní oceli na čínském automobilovém trhu? Wang li to analyzoval a řekl, že současná automobilová ocel v neustálém úsilí o snížení hmotnosti, „která využívala spoustu technologií, jeden z Příspěvkem je vysokopevnostní ocel. Zhruba posledních 20 let existuje projekt iisa, kterého se baosteel účastní. Pokud budou ocelárny nadále používat ocel vývojem nových materiálů, jaký je potenciál oceli? Díky tolika letům vývoje, poslední radě nebo technologii pro automobilový závod, je stále ještě vyvíjet různé pokročilé vysokopevnostní oceli. na cestě, druhá je vyvinout mnoho pokročilých výrobních technologií a zároveň představila koncept plného životního cyklu. Například nejnovější vývoj elektromobilu, snížení hmotnosti karoserie až o 40 %, to s vysokou pevností oceli pevnost je vyšší, více než 1000 mpa o 40%, pouze 5% je měkká ocel, ocel přes pevnost tohoto potenciálu je stále relativně velký.
„Z údajů o prodeji baosteelu vyplývá, že v roce 2017 tvořily čínské vlastní značky 41 % spotřeby vysokopevnostní oceli a prodalo se více než 28 milionů evropských, japonských, amerických a korejských vozů. Materiály poskytované baosteelem jsou relativně kvalitní a naše celostátní průměrná úroveň bude o něco nižší než tato úroveň. Aplikační poměr vysokopevnostní oceli dosahuje v průměru 42–45 % z našich údajů v loňském roce, což by mělo být relativně nízké a 60–70 % v zahraničí. Tato mezera je naším potenciálem."
Soutěž mezihliníkový plecha oceli, vynikající výhodou hliníku je nízká hustota a dosažení snížení tělesné hmotnosti v souladu s poměremoceli, nutnost ztenčení ocelového plechu. Zatímco běžné ocelové plechy mají obvykle tloušťku mezi 0,7 a 0,75 mm, dnešní superpevnostní plechy mají pouze 0,65 mm nebo tenčí a kapota nového opelu seferli má tloušťku 0,6 mm.
Podle wang li „pokud se měrná hmotnost oceli nezmění, lze hmotnost pouze snížit na tenčí, ale lze upravit hustotu. Nyní máme nový nápad, kterým je upravit hustotu oceli. Výhodou hliníku je nízká hustota, konkurence do určité míry mohu využít vašich výhod k úpravě své hustoty. Zvýšili jsme modul pružnosti oceli , a teď je to v laboratoři. Chci upozornit na to, že protože ocel samotná zůstává nezměněna na základě stávajícího průmyslového průmyslu, je zde stále velký prostor pro inovace. Z tohoto pohledu má ocel stále určitou vitalitu, stejně jako její podíl na trhu. Pokud se vůz prodá za více než 200 000 juanů, bude spotřebovávat více materiálů. Pokud se auto prodá za 100 000 juanů, bude stále používat ocel.“
Problémem s cenou se ale stává i jiný materiál, který má nahradit hlavní těleso z oceli, z tvrdého důvodu. Shu-ming Chen řekl: „V rámci trendu automobilového odlehčování, ačkoli nyní každý dělá lehké materiály, jako je hliníková slitina, hořčíková slitina a další lehké kompozitní materiály, vysokopevnostní ocel nebo v hlavní poloze těla, ale myslím, že hlavními faktory jsou náklady, věřím, že pokud náklady na uhlíková vlákna, uhlíková vlákna nahradí pravděpodobné, není to nemožné, klíčová nyní cena je příliš vysoká ocel má v současné době také velmi velkou nákladovou výhodu.“
Kromě nákladů se v rámci pevnostního rozsahu pro uspokojení poptávky stává dobrý a snadný proces tváření také důvodem, proč je obtížné ocel nahradit.“ Z vývojového hlediska je pevnost oceli pro automobil ne příliš vysoká. 1000 mpa je dost.Vysokopevnostní ocel je nyní zpevněna hlavně uhlíkem, mnozí z nich udělali 2200 mpa, ale nad 2200 mpa způsobí mutaci, nebo 2200-2500 mpa uhlík ke zpevnění je v podstatě nemožné.“ Věřím, že tato ocel určitě bude mít jiné materiály nahrazující uhlík, pevnost bude vyšší a vyšší, ale nemusí se nutně používat v autě, může být použit v jiných oblastech s vysokou pevností. Pro automobily máme široký výběr oceli pod 1000 mpa, nízké náklady a velmi dobrý proces tváření, takže nahradit ocel v naší zemi bude nějakou dobu velmi obtížné.“
A ze strukturálních vlastností samotné oceli má dobrou opravu. Zhu qiang poukázal na to, že samotná ocel s fázovým přechodem má v některých aplikacích určité výhody.“ U automobilové oceli, protože ocel má fázové přechody, pokud narazí na jámu, dá se snadno opravit, což je u kompozitů nebo hliníku poměrně obtížné. Například kompozitní materiál z hliníkové slitiny, pokud se rozbije díra, základní oprava je celý kus výměny, cena je také vysoká, to je slabina samotný hliník ve srovnání s ocelí.
Slitina hliníkuvývojové období před vlkem po tygrovi
Čísla ukazují, že k výrobě průměrného automobilu střední velikosti je zapotřebí 725 kilogramů oceli a litiny a 350 kilogramů lisované oceli. Naproti tomu hmotnost hliníku v evropském automobilu vzrostla z 50 kg v roce 1990 na 131,5 kg v roce 2005. nejvíce se stále používá v motorech a blocích válců a stoupá. Hliník je také oblíbený v autech, protože má méně než polovinu hmotnosti železa, materiálu používaného k výrobě oceli, a má lepší odolnost proti korozi než ocel.
V současnosti se při výrobě karoserie tohoto modelu často používá hliníková slitina. Od svého zrodu v roce 1994 přijalo audi A8 konstrukci karoserie s celohliníkovým prostorovým rámem a Model S vyvinul a vyrobila tesla. také přijímá celohliníkové tělo. Po celohliníkové výrobní lince chery jaguar land rover v changshu byla uvedena do výroby provincie Ťiang-su,první domácí automobil, nový jaguar XFL z hliníkové slitiny, míra aplikace materiálu dosáhla 75 %. Nobelis RC5754 vysoce pevná hliníková slitina použitá v mnoha částech karoserie jaguar XFL má výtěžnost 105-145 Mpa, pevnost v tahu 220 Mpa a dobrý výkon z hlediska pevnosti, odolnosti proti korozi, konektivity a rychlosti lisování.
"Nyní se stále více hliníku používá pro automobily, zejména pro části podvozku, kromě karoserie, nyní mnoho aut stále chodí po této silnici. Existují určité problémy s celohliníkovým rámem, ale jsou v práci." „Zhang haitao, výzkumník na univerzitě v Soochow, řekl: „Proč používat celohliníkové rámy? První náklady jsou relativně nízké, náklady na malé auto mohou být několik tisíc juanů za rám, nejdůležitější je konstrukce sekce je velmi složitý a ohyb hliníku a torzní tuhost je lepší než ocel.
Kromě toho má hliník lepší využití zdrojů a delší životní cyklus než ocel. Zhu Qiang řekl: „míra recyklačních ztrát hliníku je pouze 5 až 10 procent. Pokud je ocel zrezivělá, je velmi obtížné ji obnovit. Hliníkové slitiny mají výhody z dlouhodobého hlediska. Pokud jsou kola s hliníkem, nyní máme konsenzus, že kola z hliníkové slitiny musí být lepší než ocelová, protože ocel se snadno dotýká rzi, škrábání hliníkové slitiny nevadí, tato výkonná ocel není žádná Pro srovnání má kompozitní výkon z hliníkové slitiny v tomto ohledu jedinečnou výhodu.“ Kromě toho je pro automobilový průmysl důležitý také dlouhý životní cyklus a každý produkt musí být navržen s ohledem na dlouhý životní cyklus. Hliník má v tomto ohledu také výhodu.“
Zhu qiang také poukázal na to, že složení hliníkové slitiny je poměrně složité, a jak recyklovat klasifikaci je také problém.“ Například v rámci tlakového lití nelze použít dvě slitinové desky společně, musí být oddělené, vyžaduje hodně úsilí je propojit a oddělit je vyžaduje hodně úsilí. Na jedné straně není efektivita zpětného získávání vysoká a na druhé straně není snadné ji řídit. Kromě toho existuje mnoho problémů spojených s recyklací hliníku, jako je snížená spotřeba, dobrá recyklace hliníku vyrobit něco, co není důležité, to, co by bývalo bylo dobré, skončí s nízkou hodnotou.“
Z hlediska únavových vlastností materiálů je hliník rizikovější než ocel a zpracování je omezené.“ Únavový výkon klíčových komponentů vozidel je řízen nejen vlastnostmi samotných materiálů, ale také vadami materiály.Oxidační kapacita hliníku je velmi silná, tyto vady mají relativně velký vliv na únavové chování součástí, velmi snadno se pokazí.Ocel tolik neoxiduje a její vady mají relativně nízký dopad na únavové vlastnosti.“ Zhu qiang řekl: „Pouze s kováním nemohou být složité součásti, kování musí být zpracováno, jinak nemůže vyhovět potřebám konstrukčního návrhu. Obecně lze říci, že existují dva druhy kování, a to buď vzdání se strukturální optimalizace nebo přepracování. Jakmile je však povrch hliníkové slitiny poškozen, únavový výkon se sníží a náklady opět porostou. Toto jsou problémy, které musí hliníkové slitiny překonat, a po vyřešení těchto problémů je možné ocel nahradit.“
V automobilovém podvozku hliník nahradil část oceli, ale v posledních letech s rozvojem technologie oceli zavedla ocel podvozku nová řešení. Zhu qiang řekl: „Nyní podvozek s ocelí jsme vyvinuli několik technologií, jednou je rameno, nyní do 780 mpa můžeme nyní vyrobit ocelové trojúhelníkové rameno, je o méně než 10 procent těžší než hliník, mnohem nižší náklady. Mezi dvěma koly je také velmi těžké spojení a nyní jsme vyvinuli novou technologii, která snižuje hmotnost o 40 procent a řeší problém s korozí použitím povlaků a ocelipodílu pokročilé technologie lze dosáhnout těla bez změny o více než 10 %.“ „S některými novými technologiemi a technikami lze dosáhnout více než 20procentního úbytku hmotnosti. Analyzovali jsme mnoho modelů našich vlastních značek a potenciál je stále skvělý. Ta mezera je naší motivací