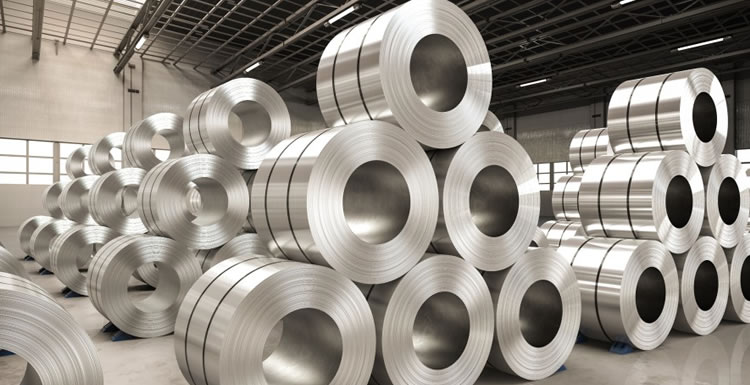
aluminijski lim konkurira čeliku
Čelik je oduvijek bio glavni materijal u proizvodnji automobila. Ali kako je društvo za zaštitu okoliša i uštedu energije sve glasnije, nacionalna politika potrošnje goriva ima tendenciju da se pooštrava, potrošači također postavljaju veće zahtjeve za sigurnost vozila, što je primoralo proizvođače automobila da tražiti jači i lakši materijal za izgradnju vozila. Očekuje se da će upotreba čelika visoke čvrstoće dostići vrhunac od skoro 15 posto težine vozila do 2020. godine, prema izvještaju centra za automobilska istraživanja. Do 2040. taj udio će postepeno pasti na skoro 5 posto, kada će drugi laki materijali imati mjesto u poslu s automobilskim materijalima.
Sa manje od polovine težine i boljom otpornošću na koroziju od sirovog materijala čelika, aluminijum je nekada predstavljao pretnju za automobilski čelik. Međutim, zbog relativno visoke cene aluminijuma i poteškoća u procesima proizvodnje i održavanja, mnogi proizvođači automobila radije zamijenite običan čelik ugljičnim čelikom visoke čvrstoće. Stoga se igra između čelika i aluminijuma. Na nedavno održanom automobilskom i ekološkom forumu, stručnjaci iz industrije kao što su Wang Li, glavni istraživač Baosteel istraživačkog instituta, Zhu Qiang, profesor na katedri Južnog univerziteta za nauku i tehnologiju, Chen Shuming, profesor jilin univerziteta, zhang haitao i tako dalje, razgovarali su o „takmičenju čelika i aluminijuma“ na okruglom stolu.
Čelik ima veliki potencijal primjene i prednost u cijeni
Uz kontinuirani razvoj automobilskog čelika, automobilski čelik je prije nekoliko desetljeća bio utisak mnogih ljudi o čeliku s niskim udjelom ugljika, sada se automobilska čelična ploča stanji, ali je čvrstoća čelika i otpornost na koroziju uvelike poboljšana. Kako bi se odgovorilo na izazov novih materijala, mnoga preduzeća za proizvodnju čelika aktivno razvijaju lagani čelik visoke čvrstoće koji može da se takmiči sa legurama aluminijuma i drugim materijalima. Prema podacima, samo 212 evra dodatnih troškova po vozilu za čelik visoke čvrstoće potrebno je da bi se postigao gubitak težine i goriva ušteda od oko 5%.
Kakva je trenutna situacija i potencijal primjene čelika visoke čvrstoće na kineskom automobilskom tržištu? Wang li je analizirao ovo, rekao je da je trenutni automobilski čelik u stalnim naporima da se smanji težina, „koji koristi puno tehnologije, jedan od doprinos je čelik visoke čvrstoće. U posljednjih 20-ak godina postojao je iisa projekat u kojem Baosteel sudjeluje. Ako čeličane nastave koristiti čelik razvijajući nove materijale, kakav je potencijal čelika? Kroz toliko godina razvoja, posljednji savjet ili tehnologija tvornici automobila je da se razvije niz naprednih čelika visoke čvrstoće i dalje na putu, drugi je razvoj mnogih naprednih proizvodnih tehnologija, a istovremeno je uveden koncept punog životnog ciklusa. Na primjer, najnoviji razvoj električnog koncept automobila, smanjenje tjelesne težine do 40%, to s visokom čvrstoćom čelika čvrstoća je veća, više od 1000 mpa od 40%, samo 5% je meki čelik, čelik kroz snagu ovog potencijala je još uvijek relativno velika.
“Prema podacima o prodaji baosteela, kineski brendovi u vlastitom vlasništvu činili su 41% potrošnje čelika visoke čvrstoće u 2017. godini, a prodano je više od 28 miliona europskih, japanskih, američkih i korejskih automobila u vlastitom vlasništvu. Materijali koje nudi baosteel su relativno visokog kvaliteta, a naš nacionalni prosjek će biti malo niži od ovog nivoa. Omjer primjene čelika visoke čvrstoće dostiže u prosjeku 42-45% prema našim podacima iz prošle godine, što bi trebalo biti relativno niske, a 60-70% u inostranstvu. Ovaj jaz je naš potencijal.”
Takmičenje izmeđualuminijumski limi čelik, izuzetna prednost aluminijuma je niska gustina i da bi se postigla smanjenje telesne težine, u skladu sa proporcijomod čelika, potreba za tanjivanjem čelične ploče. Dok su obični čelični limovi obično debljine između 0,7 i 0,75 mm, današnji limovi super čvrstoće su samo 0,65 mm ili tanji, a hauba novog Opel seferlija je debljine 0,6 mm.
Prema Wang Liju, „ako se specifična težina čelika ne promijeni, težina se može smanjiti samo na tanje, ali se gustoća može podesiti. Sada imamo novu ideju da uradimo, a to je da prilagodimo gustinu čelika. Prednost aluminijuma je niska gustina, konkurencija u određenoj meri mogu da iskoristim vaše prednosti da prilagodim svoju gustinu. Povećali smo modul elastičnosti čelika , a sada je u laboratoriji. Jedna stvar koju želim naglasiti je da zbog toga što sam čelik ostaje nepromijenjen na osnovu postojeće industrijske industrije, još uvijek ima puno prostora za inovacije. Iz ove perspektive, čelik još uvijek ima određenu vitalnost, kao i svoj tržišni udio. Ako se automobil proda za više od 200.000 juana, koristit će više materijala. Ako se automobil proda za 100.000 juana, i dalje će koristiti čelik.”
Ali problem troškova također postaje drugi materijal koji će zamijeniti glavni položaj tijela od čelika tvrdog razloga. Shu-ming Chen je rekao, „pod trendom automobilske lagane težine, iako sada svi rade lagane materijale, poput legure aluminija, legure magnezija i drugih lagani kompozitni materijali, čelik visoke čvrstoće ili u glavnom položaju tijela, ali mislim da je glavni faktor cijena, vjerujem da ako će cijena karbonskih vlakana, karbonska vlakna zamijeniti vjerovatno, nije nemoguće, ključna cijena je sada previsoko, čelik trenutno takođe ima veoma veliku prednost u pogledu troškova.”
Osim cijene, unutar raspona čvrstoće za zadovoljavanje potražnje, dobar i lak proces oblikovanja također postaje razlog zašto je čelik teško zamijeniti.” Sa razvojne tačke gledišta, snaga čelika za automobil je nije jako visoka. 1000 mpa je dovoljno. Čelik visoke čvrstoće je sada uglavnom ugljik za jačanje, mnogi su radili 2200 mpa, ali iznad 2200 mpa će proizvesti mutaciju, ili 2200-2500 mpa ugljika za jačanje u osnovi nemoguće.” Vjerujem da će ovaj čelik definitivno imati drugi materijali za zamjenu ugljika, snaga će biti sve veća i veća, ali ne mora se koristiti u automobilu, može se koristiti u drugim područjima visoke čvrstoće. Za automobile imamo širok izbor čelika ispod 1000 mpa, niske trošak i vrlo dobar proces oblikovanja, tako da će kod nas neko vrijeme biti vrlo teško zamijeniti čelik.”
A što se tiče strukturnih svojstava samog čelika, ima dobru popravku. Zhu qiang je istakao da sam čelik sa faznim prijelazom ima neke prednosti u nekim primjenama.” Za automobilski čelik, jer čelik ima fazne prijelaze, ako udari u jamu, može se lako popraviti, što je relativno teško za kompozite ili aluminijum. Na primjer, kompozitni materijal od legure aluminija, ako je rupa pukla, osnovna popravka je cijeli komad zamjene, cijena je također visoka, to je slabost sam aluminijum u poređenju sa čelikom.
Aluminijska leguraPeriod razvoja nastao prije Vuka nakon tigra
Brojke pokazuju da je potrebno 725 kilograma čelika i livenog gvožđa i 350 kilograma štancanog čelika da bi se napravio prosečni automobil srednje veličine. Nasuprot tome, težina aluminijuma u evropskom automobilu porasla je sa 50 kg 1990. na 131,5 kg 2005. godine, sa većina se još uvijek koristi u unutrašnjosti motora i blokovima cilindara i raste. Aluminij je također popularan u automobilima jer je manje od polovine težine željeza, materijala koji se koristi za izradu čelika, i ima bolju otpornost na koroziju od čelika.
Trenutno je upotreba aluminijumske legure za izradu karoserije modela bila velika. Od svog rođenja 1994. godine, audi A8 je usvojio potpuno aluminijumsku strukturu svemirskog okvira, a Model S je razvio i proizveo Tesla također usvaja potpuno aluminijsku karoseriju. Nakon potpuno aluminijumske proizvodne linije Chery Jaguar Land Rover u Čangšuu, provincija Jiangsu je puštena u proizvodnju,prvi domaći automobil, novi jaguar XFL materijal od legure aluminijuma, stopa primene materijala dostigla je 75%. Nobelis RC5754 aluminijumska legura visoke čvrstoće koja se koristi u mnogim delovima karoserije jaguara XFL ima prinos od 105-145 Mpa, vlačnu čvrstoću od 220 Mpa , i dobre performanse u čvrstoći, otpornosti na koroziju, povezanosti i brzini oblikovanja.
„Sada se sve više aluminijuma koristi za automobile, posebno za delove šasije, pored karoserije, sada dosta automobila nastavlja da hoda ovim putem. Postoje neki problemi sa potpuno aluminijumskim okvirom, ali oni se rešavaju .”Zhang haitao, istraživač na soochow univerzitetu, rekao je, “zašto koristiti potpuno aluminijumske okvire? Prvi trošak je relativno nizak, cijena malog automobila može biti nekoliko hiljada juana po okviru, najvažniji je dizajn odjeljka je vrlo složen, a aluminijumska krutost na savijanje i torziona je bolja od čelika.
Osim toga, aluminijum ima bolji oporavak resursa i duži životni ciklus od čelika. Zhu qiang je rekao: „Stopa gubitka aluminijuma pri recikliranju je samo 5 do 10 procenata. Ako je čelik zarđao, vrlo ga je teško oporaviti. Aluminijumske legure imaju prednosti na duge staze. Ako su felge sa aluminijumom, sada imamo konsenzus da felge od aluminijumske legure moraju biti bolje od čelika, jer čelik lako dodiruje hrđu, struganje od aluminijumske legure nije bitno, ovaj čelik performansi nije Za usporedbu, performanse kompozita od aluminijske legure u ovom pogledu imaju jedinstvenu prednost.” Osim toga, dug životni ciklus je važan i za automobilsku industriju, a svaki proizvod mora biti dizajniran imajući na umu dug životni ciklus. Aluminijum takođe ima prednost u ovom pogledu.”
Zhu qiang je također istakao da je sastav legure aluminija relativno složen, a kako reciklirati klasifikaciju je također problem.” Na primjer, za okvir tlačnog livenja, dvije ploče od legure ne mogu se koristiti zajedno, one moraju biti razdvojeni, potrebno je mnogo truda da se oni povežu, a potrebno je mnogo truda da se razdvoje. S jedne strane, efikasnost oporavka nije visoka, as druge strane, nije lako upravljati. Osim toga, postoji mnogo problema vezanih za recikliranje aluminijuma, kao što je smanjena upotreba, može se koristiti dobra reciklaža aluminijuma da nešto što nije važno, ono što bi bilo dobro završi sa niskom vrednošću.”
Što se tiče svojstava materijala na zamor, aluminijum je rizičniji od čelika, a obrada je ograničena.” Performanse zamora ključnih komponenti vozila kontrolišu se ne samo osobinama samih materijala, već i defektima materijala. materijali. Kapacitet oksidacije aluminijuma je veoma jak, ovi defekti imaju relativno veliki uticaj na performanse zamora komponenti, vrlo je lako pogrešiti. Čelik ne oksidira toliko i njegovi defekti imaju relativno mali uticaj na performanse zamora.” Zhu qiang rekao je, „samo kod kovanja ne mogu biti složene komponente, kovanje se mora obraditi, inače ne može zadovoljiti potrebe konstrukcijskog dizajna. Uopšteno govoreći, postoje dvije vrste kovanja, ili odustajanje od strukturalne optimizacije ili ponovna obrada. Međutim, kada se površina aluminijske legure ošteti, učinak zamora će se smanjiti, a cijena će ponovo porasti. To su problemi koje aluminijske legure moraju prevladati, a nakon rješavanja ovih problema moguće je zamijeniti čelik.”
U automobilskoj šasiji, aluminij je zamijenio nešto čelika, ali posljednjih godina s razvojem tehnologije čelika, čelik šasije je uveo nova rješenja. Zhu qiang je rekao: „Sada šasija sa čelikom, razvili smo nekoliko tehnologija, jedna je ruka, mi sada do 780 mpa sada možemo napraviti čeličnu trokutnu ruku, manje je od 10 posto teža od aluminija, mnogo niža cijena. Postoji i veza između dva točka koja je vrlo teška, a sada smo razvili novu tehnologiju koja smanjuje težine za 40 posto i rješava problem korozije korištenjem premaza i čelikasama se poboljšava. Sada se čelik i aluminijum takmiče da promovišu jedni druge, tako da postoji više opcija za auto kompanije, a samim tim i razvoj.”
Zapravo, sadašnji automobilski aluminij je ušao u fazu prije Vuka nakon tigra. Bivši proizvođači čelika kroz kontinuirano poboljšanje performansi, sada čelik bez nikla može postići rđu, dok drugi od legure magnezija, karbonskih vlakana i drugih materijala sa nižim troškovima i poboljšane performanse, uticali su na tržište aluminijuma. Zhu qiang je istakao, „aluminijumska legura da bi bila dobra može biti samo brzi razvoj, jer čelik je radio toliko godina da ga zameni je teško, aluminijum mora biti industrijalizacija kao što je prije moguće, neće biti lako zamijeniti kasnije, trenutni automobilski aluminijski izazovi i prilike koegzistiraju.
Čelik-aluminijum hibridna struktura karoserije je trend
Trenutno, sve više inžinjera u proizvodnji automobila posvećuje više pažnje hibridnoj primjeni lakih materijala. Njihov fokus istraživanja i razvoja nije samo na specifičnom omjeru automobilskog čelika i aluminija, već i na tome kako pravilno pomiješati različite materijale. Prošle godine na sajmu automobila u Frankfurtu debi na novom audiju A8 bio je audijev aluminijski prostorni okvir. struktura karoserije tehnologija inovacija i nadogradnja, napušten audi je uvijek bio ponosan na cijelu aluminijsku karoseriju, aluminijsku leguru nagiba do 58%, pored identiteta, u materijal karoserije dodano više kompozitnih materijala, karoserija je skoro 51 kilogram teži od gotovinskog modela, kod keš A8 modela od 236 kg “suprotne težine do 282 kg.
Nova generacija Audija A8 koristi aluminijsku leguru za izgradnju cjelokupnog okvira karoserije. Kako bi se osigurala čvrstoća konstrukcije, aluminijski odljevci se koriste u ključnim spojevima, a dijelovi od lima se koriste na površini karoserije. U kaveznoj strukturi karoserije, veliki broj vruće oblikovanih legiranih čelika visoke čvrstoće, daleko više od trenutnog A8 čelik visoke čvrstoće samo u primjeni B stupca, čeličnog materijala visoke čvrstoće i prije 20 godina u poređenju sa čelikom, krutost je povećana 5 puta, težina smanjena za 40%. U strukturu karoserije dodana je legura magnezija, a CFRP karbonska vlakna Kompozitni materijal se koristi u stražnjem dijelu automobila, što smanjuje težinu karoserije od takvih detalja kao što je stražnja ploča.
„U budućnosti će se aluminijum sve više koristiti u celoj karoseriji automobila, a biće i mnogo hibridnih karoserija. Na primer, audi A8 aluminijumska karoserija počinje da pravi i hibridne karoserije, a sada to slede mnoge domaće auto kompanije. Glavni problem kod čeličnih i aluminijumskih spojeva je otpornost na koroziju, sa lepljenjem, sa vezom, bez zavarivanja. od čelika, a donji deo tela je napravljen od aluminijuma. Na primer, okvir prozora automobila u Pekingu je napravljen od čelika na vrhu i aluminijuma na dnu. Nije da je čelik loš, ali mislim da je više obećavajuće mešati čelik sa aluminijumom. “, rekao je Zhang haitao.
S tim u vezi, Wang li je također istakao da je zapravo, već 1940-ih godina kada je postojala konkurencija čelika i aluminija, nakon mnogo godina razvoja, sada su automobilski materijali postigli određeni konsenzus, pravi materijali koji se koriste na pravom mjestu .I sam čelik se brzo razvija, i konkurencijom i saradnjom. I ova konkurencija je korisnija za razvoj automobilskih preduzeća, jer postojanje konkurencije automobilska preduzeća mogu imati više izbora. Gledajući u budućnost, nova energetska vozila mogu imati veću zahtjevi za laganu težinu.
Strategija „nezavisnih brendova mora biti lagana, dobar čelik sa svojim potencijalom još uvek nije mali, uz pomoć zajedničkih ulaganja brendova sa udelom čelika visoke čvrstoće i vrlo je lako postići 10% gubitka telesne težine belog, kroz napori drugih vozila pad 7% 8% je izvodljivo, identitetudio napredne tehnologije može postići tijelo bez promjene od više od 10%.””Uz neke nove tehnologije i tehnike može se postići gubitak težine više od 20 posto. Analizirali smo mnoge modele vlastitih brendova, te potencijal je i dalje odlično. Jaz je naša motivacija